-
Gebäude E, Nr. 65 Xingshan North Road, Liangtian, Baisha Industrial Park, Bezirk Baiyun, Guangzhou
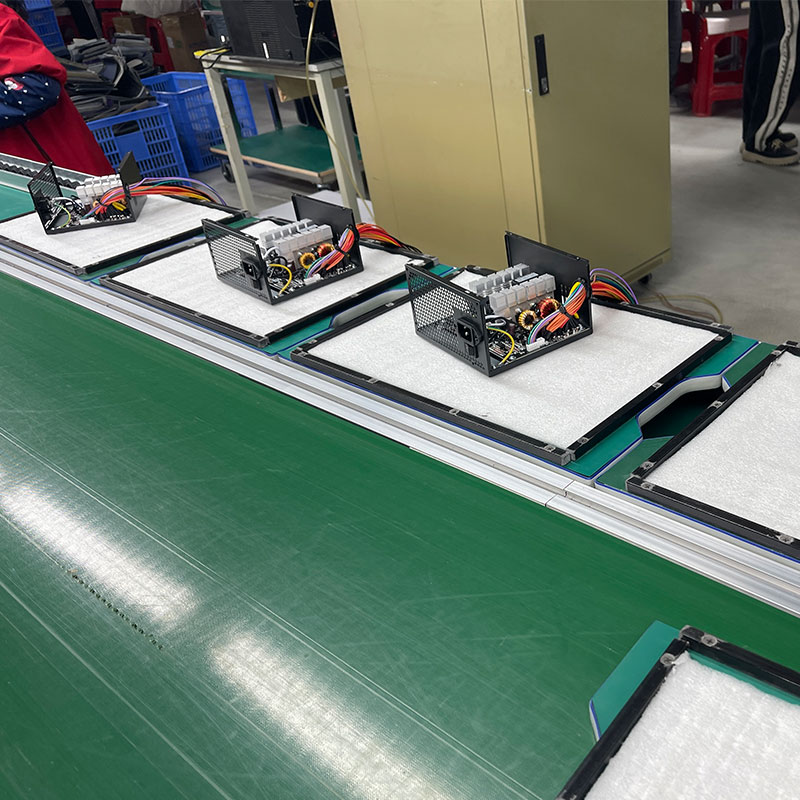
9 Schritte zur Herstellung eines Tischnetzteils
Der Produktionsprozess eines Desktop-Netzteils (PC Power Supply Unit, PSU) umfasst mehrere Schritte, darunter die Montage elektronischer Komponenten, das Schaltungsdesign, Sicherheitstests usw. Im Folgenden finden Sie 9 Schritte zur Herstellung eines Tischnetzteils:
1. Design und Entwicklung
Schaltungsaufbau:
Das Design und die Entwicklung von Desktop-Netzteilen ist der Ausgangspunkt des Produktionsprozesses und bestimmt direkt die Leistung, Effizienz und Zuverlässigkeit des Produkts. Zunächst müssen die Ingenieure die Eingangs- und Ausgangsparameter des Netzteils gemäß Industriestandards (z. B. Intel ATX-Spezifikationen) definieren, einschließlich Nennleistung (z. B. 500 W, 750 W), Spannungsbereich (+12 V, +5 V, +3,3 V usw.) und Schnittstellentyp (24-poliges Motherboard-Netzteil, PCIe 8-polig usw.). Das Kernschaltungsdesign verwendet normalerweise die Architektur „aktive PFC+LLC-Resonanz+Synchrongleichrichtung“, um eine hohe Umwandlungseffizienz (z. B. 80 PLUS Goldmedaille oder höher) zu erreichen. In dieser Phase muss die Stabilität der Topologiestruktur mithilfe einer Simulationssoftware (z. B. SPICE) überprüft werden, um sicherzustellen, dass die Spannung unter extremen Bedingungen wie Lastmutation und hohen Temperaturen stabil bleiben kann.
Komponentenauswahl: Wählen Sie Schlüsselkomponenten (wie Kondensatoren, Induktoren, MOSFETs, Transformatoren, Kühlkörper usw.) unter Berücksichtigung von Effizienz (wie 80 PLUS-Zertifizierung), Leistungsdichte und Kosten aus.
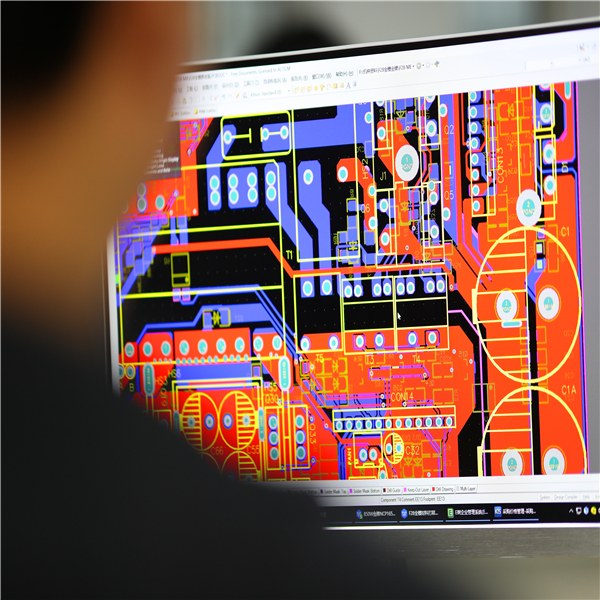
Simulationsüberprüfung:
Bei der Auswahl der Komponenten müssen bei Schlüsselkomponenten sowohl Leistung als auch Kosten berücksichtigt werden: Der Hauptsteuerchip besteht meist aus taiwanesischen (z. B. Great Wall) oder amerikanischen (z. B. Texas Instruments) Lösungen; Kondensatoren müssen eine hohe Temperaturbeständigkeit (über 105 °C) und eine lange Lebensdauer aufweisen (z. B. japanische Nippon Chemi-Con); und Kühllüfter müssen Geräusche (<25 dB) und Luftvolumen ausgleichen. Darüber hinaus muss das Designteam das PCB-Layout optimieren, z. B. den Hochspannungsbereich (Primärseite) vom Niederspannungsbereich (Sekundärseite) isolieren, elektromagnetische Interferenzen (EMI) reduzieren und Impedanz und Wärmeverlust durch mehrschichtige Verdrahtung verringern.
Leiterplattenlayout:
In der Entwurfsphase müssen auch Zertifizierungsanforderungen (wie UL, CE, FCC) vorhergesagt werden, um zu vermeiden, dass EMI den Standard überschreitet oder das Risiko von Isolationsfehlern im Voraus besteht. Beispielsweise müssen Sicherheitsabstände (Kriechstrecken und elektrische Abstände) dem IEC 60950-Standard entsprechen, und die PFC-Schaltung muss die Oberwellengrenzwerte von IEC 61000-3-2 einhalten. Schließlich werden die Entwurfsdokumente (einschließlich Schaltpläne, Stücklisten und 3D-Strukturmodelle) in die Produktionsphase übertragen, um genaue Richtlinien für die anschließende Materialbeschaffung und Montage bereitzustellen. Dieser Prozess dauert in der Regel mehrere Monate bis ein halbes Jahr und ist die Grundlage der Stromqualität.
2. Rohstoffbeschaffung und -prüfung
Die Beschaffung und Prüfung von Rohmaterialien sind entscheidende Schritte bei der Produktion von PC-Netzteilen, die sich direkt auf die Produktqualität und -zuverlässigkeit auswirken. Bei der Beschaffung von Komponenten kontrollieren wir streng die Qualität von Schlüsselkomponenten wie Elektrolytkondensatoren, PFC-Induktoren, Haupttransformatoren, IC-Steuerchips und Lüftern, die den Kern der Netzteilleistung bilden. Die von uns gekauften Rohmaterialien müssen den RoHS-Umweltstandards entsprechen, um den Umweltschutz und die Nachhaltigkeit der Produkte zu gewährleisten.
Die Wareneingangsprüfung (IQC) ist der Schlüssel, um sicherzustellen, dass alle Komponenten, die in die Produktionslinie gelangen, den Qualitätsstandards entsprechen. Wir führen umfassende Qualitätsprüfungen an Komponenten durch, einschließlich der Kapazität und Spannungsfestigkeit von Kondensatoren, des Einschaltwiderstands von MOSFETs und anderer wichtiger Parameter, um sicherzustellen, dass sie die Designanforderungen vollständig erfüllen. Unser IQC-Prozess ist streng und sorgfältig, und jede Rohstoffcharge wird streng geprüft, um zu verhindern, dass nicht qualifizierte Komponenten in den Produktionsprozess gelangen. Auf diese Weise wird die hervorragende Qualität und langfristige Zuverlässigkeit des Endprodukts sichergestellt. Dies hilft uns, die Produktqualität zu gewährleisten und bessere Dienstleistungen anzubieten.
3. Leiterplattenherstellung
Die PCB-Produktion (Printed Circuit Board) ist das Kernstück der PC-Netzteilherstellung. Sie bietet zuverlässige Verbindung und Unterstützung für elektronische Komponenten, genau wie das „Skelett“ des Netzteils. Unser PCB-Produktionsprozess folgt streng den Industriestandards, um sicherzustellen, dass jede PCB hervorragende Leistung und Haltbarkeit aufweist.
Substratherstellung:
Wir wählen hochwertige Isoliersubstrate wie FR-4 oder höherwertige Materialien aus, die über hervorragende elektrische Isoliereigenschaften und mechanische Festigkeit verfügen. Kupferfolie wird auf das Isoliersubstrat laminiert, um ein PCB-Substrat zu bilden. Die Dicke der Kupferfolie beträgt normalerweise zwischen 1 Unze (ca. 35 Mikrometer) und 2 Unzen (ca. 70 Mikrometer), und die konkrete Wahl hängt vom Auslegungsstrom und Spannungsniveau der Stromversorgung ab.
Fotolithografie und Ätzen:
Wir verwenden Fotolithografie, um das Schaltungsmuster auf das PCB-Substrat zu übertragen. Dies ähnelt dem Prozess der Entwicklung eines Fotos, bei dem das lichtempfindliche Material entsprechend dem Schaltplan belichtet wird. Durch Ätzen entfernen wir die überschüssige Kupferschicht und hinterlassen die erforderlichen Leiterbahnen und Pads, wodurch das „Blutgefäßsystem“ der Stromversorgung entsteht. Die Ätzgenauigkeit kann normalerweise 0,1 mm oder weniger erreichen, um den Anforderungen eines Schaltungsdesigns mit hoher Dichte gerecht zu werden.
Bohren und Kupferabscheidung:
Dies ist ein wichtiger Schritt bei der Herstellung von Leiterplatten. Wir verwenden hochpräzise Bohrgeräte, um Durchgangslöcher (Vias) und Bauteilstiftlöcher in Leiterplatten zu bohren. Durchgangslöcher werden verwendet, um verschiedene Leiterplattenschichten zu verbinden und Kanäle für die Stromübertragung bereitzustellen. Beim Verkupferungsprozess wird eine Kupferschicht auf die Wand des gebohrten Lochs aufgebracht, um die Leitfähigkeit des Durchgangslochs sicherzustellen. Die Kontrolle der Lochgröße und des Lochabstands ist für die elektrische Leistung der Leiterplatte von entscheidender Bedeutung. Beispielsweise beträgt der Durchmesser des Durchgangslochs normalerweise zwischen 0,3 mm und 0,6 mm, um den Anforderungen der Stromübertragung gerecht zu werden.
Lötstopplack und Siebdruck:
Wir tragen Lötstopplacktinte, normalerweise grün oder in anderen Farben, auf die Oberfläche der Leiterplatte auf, um die Leiterbahnen vor Korrosion und Kurzschlüssen zu schützen. Der Lötstopplack wird auch verwendet, um den Lötbereich des Bauteils zu definieren. Als Nächstes drucken wir die Bauteilidentifikation auf die Leiterplatte, beispielsweise die Anzahl der Widerstände und Kondensatoren, um die nachfolgende Bauteilmontage und Wartung zu erleichtern. Die Dicke des Lötstopplacks beträgt im Allgemeinen zwischen 15 und 30 Mikrometer, um einen guten Schutz der Schaltung zu gewährleisten. Nach diesen strengen Prozessen erreicht jede Leiterplatte optimale Leistung.
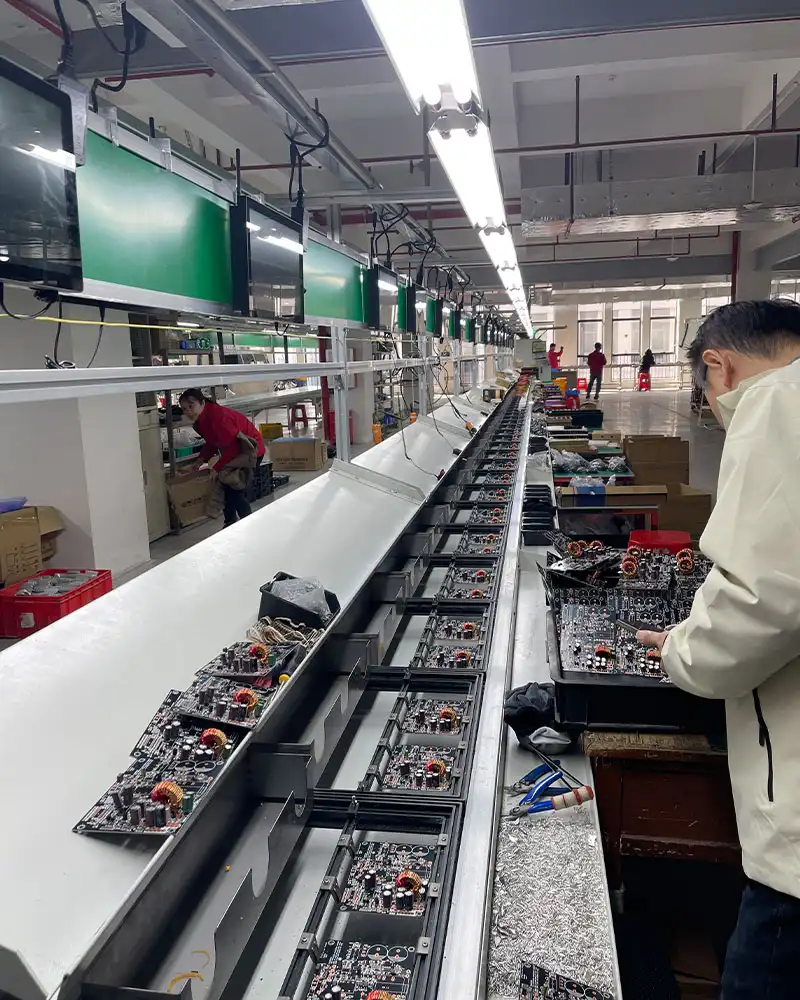
4. Komponenteninstallation
Dies ist ein wichtiger Schritt bei der Montage von PC-Netzteilen. Es verbindet das „Skelett“ auf der Leiterplatte mit verschiedenen elektronischen Komponenten und bildet so das „Herz“ des Netzteils. Unser Komponenteninstallationsprozess verwendet fortschrittliche SMT (Surface Mount Technology) und traditionelle Plug-in-Technologie, um eine genaue Installation und zuverlässige Verbindung der Komponenten zu gewährleisten.
SMT-Patch:
Mithilfe hochpräziser Patchmaschinen löten wir kleine Komponenten wie Widerstände, Kondensatoren, IC-Chips usw. präzise auf die Pads der Leiterplatte. Die Patchmaschine kann schnelles und hochpräzises Patchen erreichen, und die Patchgenauigkeit kann normalerweise 0,1 mm erreichen. Anschließend verwenden wir das Reflow-Lötverfahren, um die Lötpaste zu schmelzen, sodass die Komponenten fest auf der Leiterplatte befestigt sind. Die Temperaturkurve des Reflow-Lötens wird präzise gesteuert, um die Qualität des Schweißens sicherzustellen.
Komponenteninstallation:
Es ist für große Komponenten wie Elektrolytkondensatoren, Transformatoren und Kühlkörperstifte geeignet. Diese Komponenten sind normalerweise groß und können nicht per SMT gepatcht werden. Unsere Mitarbeiter setzen diese Komponenten während des Einsteckvorgangs manuell oder maschinell in die entsprechenden Löcher der Leiterplatte ein. Das manuelle Einstecken gewährleistet Flexibilität und Präzision der Installation, während das maschinelle Einstecken die Effizienz und Konsistenz verbessert.
Wellenlöten:
Löten von Steckkomponenten, um zuverlässige elektrische Verbindungen herzustellen. Beim Wellenlöten wird die Leiterplatte in geschmolzenes Lot getaucht, sodass das Lot die Bauteilstifte benetzt und Lötstellen bildet. Temperatur und Zeit des Wellenlötens werden präzise kontrolliert, um die Lötqualität sicherzustellen. Durch diese strengen Prozesse wird jedes Netzteil mit optimaler Leistung zusammengebaut.
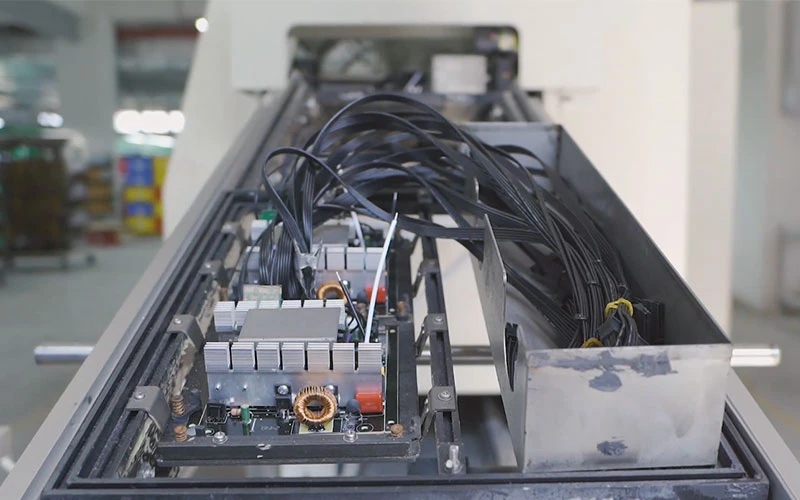
5. Montage des Schlüsselmoduls
Es ist das Kernstück der PC-Netzteilherstellung. Diese Module bestimmen direkt die Leistung, Effizienz und Zuverlässigkeit des Netzteils. Wir verwenden bei der Montage der Schlüsselmodule präzise Prozesse und strenge Qualitätskontrollen, um sicherzustellen, dass jedes Modul optimale Leistung erzielen kann.
PFC-Modul (Power Factor Correction):
Wir installieren aktive oder passive Leistungsfaktorkorrekturschaltungen, um die Stromnutzung zu verbessern. Aktive PFC-Schaltungen können den Leistungsfaktor der Stromversorgung deutlich auf nahezu 1 verbessern, wodurch Blindleistungsverluste im Stromnetz reduziert und Energieeffizienzstandards eingehalten werden. Wir stellen die Qualität und Installation wichtiger Komponenten wie PFC-Induktoren sicher, um die Leistung von PFC-Modulen sicherzustellen.
Haupttransformator und Gleichrichtermodul:
Wir montieren Hochfrequenztransformatoren zur Trennung von Wechselstrom und zur Spannungsanpassung. Qualität und Design des Transformators sind entscheidend für die Effizienz und Stabilität des Netzteils. Gleichzeitig montieren wir auch Gleichrichterschaltungen, wie Synchrongleichrichter oder Schottky-Dioden. Diese Komponenten dienen zur Umwandlung von Wechselstrom in Gleichstrom, um die erforderliche Spannung für verschiedene Komponenten des Computers bereitzustellen. Die richtige Auswahl und Installation dieser Komponenten sind entscheidend für die Ausgangsqualität des Netzteils.
Kühlsystem:
Da das Netzteil während des Betriebs Wärme erzeugt, ist das Kühlsystem von entscheidender Bedeutung. Wir befestigen den Kühlkörper, der normalerweise aus einer Aluminiumlegierung besteht, um die Wärmeableitungsfläche zu vergrößern. Wir verwenden außerdem wärmeleitendes Silikon, um die Wärmeleitung zwischen dem Kühlkörper und dem Heizelement zu verbessern. Darüber hinaus installieren wir einen Kühllüfter, normalerweise einen 12-cm- oder 14-cm-Lüfter, um eine effektive Luftzirkulation zu gewährleisten, Wärme aus dem Inneren des Netzteils abzuführen und einen stabilen Betrieb des Netzteils zu gewährleisten.
6. Montage des Leistungsmoduls
Dies ist der letzte Prozess der PC-Netzteilherstellung, bei dem alle internen Komponenten zu einem vollständigen und nutzbaren Netzteil zusammengefügt werden. In diesem Zusammenhang achten wir auf jedes Detail, um die Sicherheit, Stabilität und Schönheit des Netzteils zu gewährleisten.
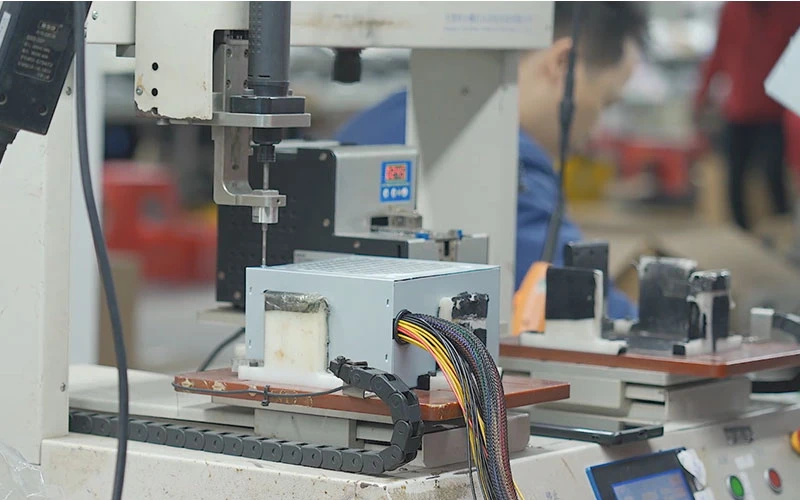
Gehäusemontage:
Wir installieren interne Komponenten wie PCB (Leiterplatte), Lüfter, Schalter usw. in das Metallgehäuse, das normalerweise aus verzinktem Stahlblech besteht, um einen soliden Schutz und eine gute EMI-Abschirmung (elektromagnetische Interferenz) zu bieten. Die EMI-Abschirmung kann wirksam verhindern, dass elektromagnetische Strahlung im Netzteil andere elektronische Geräte stört, und die Auswirkungen externer elektromagnetischer Interferenzen auf das Netzteil verringern. Während des Gehäusemontageprozesses stellen wir sicher, dass alle Komponenten fest im Gehäuse befestigt und fest mit dem Gehäuse verbunden sind.
Kabelschweißen:
Wir werden verschiedene Ausgangskabel anschließen, darunter 24-polige Motherboard-Stromversorgung, PCIe-Stromversorgung, SATA-Stromversorgung usw., die zur Stromversorgung verschiedener Komponenten des Computers verwendet werden. Die Qualität der Schweißung steht in direktem Zusammenhang mit der Stabilität und Zuverlässigkeit der Stromversorgung. Wir verwenden hochwertige Schweißmaterialien und -verfahren, um sicherzustellen, dass die Schweißpunkte fest und zuverlässig sind. Nach dem Schweißen werden wir Isolierhüllen auf die Kabel aufbringen, um Kurzschlüsse und andere Sicherheitsrisiken zu vermeiden.
Befestigung und Isolierung:
Wir befestigen die internen Komponenten mit Schrauben, um zu verhindern, dass sie sich während des Transports oder der Verwendung bewegen oder lösen. Um die Sicherheit der Stromversorgung weiter zu verbessern, fügen wir außerdem Isolierfolien oder Gummipolster hinzu, um Kurzschlüsse zwischen internen Komponenten zu verhindern. Das Material und die Dicke der Isolierfolie werden sorgfältig ausgewählt, um eine gute Isolierung zu gewährleisten. Durch diese Prozesse erreicht jedes Leistungsmodul eine sichere, stabile und zuverlässige Wirkung.
7. Prüfung und Kalibrierung
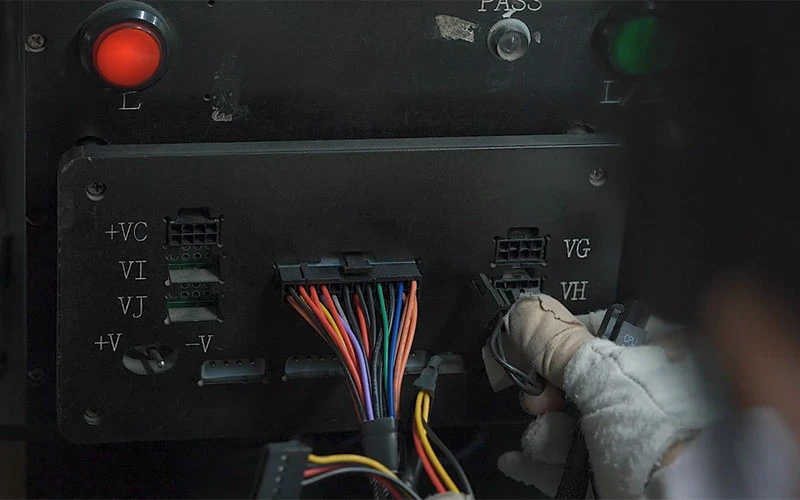
Einschalttest:
Überprüfen Sie, ob die Leerlaufspannung und die Standby-Stromversorgung (+5VSB) normal sind.
Belastungstest: Simulieren Sie den Volllastbetrieb, um die Stabilität jedes Spannungsausgangs (+12 V, +5 V, +3,3 V) zu überprüfen.
Schutzfunktionstest:
Trigger-Überspannungsschutz (OVP), Überstromschutz (OCP), Kurzschlussschutz (SCP) usw.
Wirkungsgrad- und Welligkeitstest:
Messen Sie die Umwandlungseffizienz (z. B. 80 PLUS-Zertifizierungsanforderungen) und die Ausgangswelligkeit (muss den Intel ATX-Standards entsprechen).
Burn-In-Test: Mehrere Stunden kontinuierlich laufen lassen, um frühzeitig fehlerhafte Komponenten zu erkennen.
8. Zertifizierung und Konformitätsprüfung
Sicherheitszertifizierung: Bestehen Sie UL-, CE-, FCC-, CCC- und andere Zertifizierungen, um die Einhaltung regionaler Sicherheitsstandards zu gewährleisten.
Energieeffizienz-Zertifizierung: Beantragen Sie die 80 PLUS-Zertifizierung (Bronze/Gold/Titan usw.) und kennzeichnen Sie den Effizienzgrad.
EMI/EMV-Test: Stellen Sie sicher, dass die elektromagnetische Strahlung den Vorschriften entspricht, um Störungen anderer Geräte zu vermeiden.
9. Verpackung und Versand
Optische Prüfung: Reinigen Sie das Gehäuse und prüfen Sie es auf Kratzer oder Montagefehler.
Zubehörverpackung: Netzkabel, Schrauben, Handbuch usw. sind im Lieferumfang enthalten.
Barcode und Rückverfolgbarkeit: Zur einfachen Rückverfolgbarkeit der Qualität ist ein Etikett mit der SN-Seriennummer angebracht.
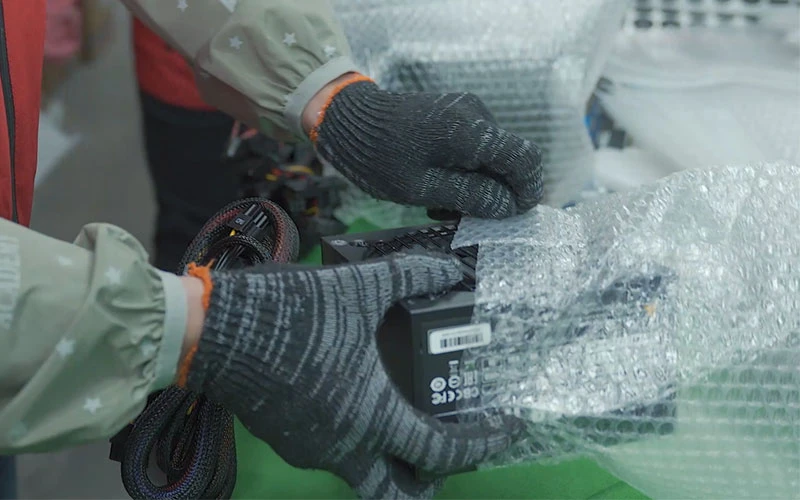
Wichtige Punkte der Qualitätskontrolle
Dies sind die 9 Schritte zur Herstellung eines Tischnetzteils. Darüber hinaus müssen folgende Punkte beachtet werden:
Lebensdauer des Kondensators: Wählen Sie hochwertige japanische oder taiwanesische Kondensatoren (z. B. Rubycon, Nippon Chemi-Con).
Wärmeableitungsdesign: Gleichen Sie Lüftergeschwindigkeit und Geräuschentwicklung aus, um eine langfristige Temperaturkontrolle zu gewährleisten.
Schweißqualität: Vermeiden Sie schlechten Kontakt durch Fehllötungen und Kaltlötungen.
Branchentrends
Miniaturisierung und hohe Leistungsdichte: So passt sich beispielsweise das SFX-Netzteil an kleine Hosts an.
Digitale Steuerung: Verwenden Sie einen digitalen Signalprozessor (DSP), um eine intelligente Spannungsregelung zu erreichen.
Vollständig modulares Design: Benutzer können Kabel individuell anpassen, um Unordnung im Gehäuse zu vermeiden.
Im Rahmen des oben genannten Prozesses müssen Desktop-Netzteile vom Entwurf bis zum fertigen Produkt strengen Prozesskontrollen und Tests unterzogen werden, um ihre Zuverlässigkeit, Effizienz und Sicherheit zu gewährleisten. Verschiedene Marken können sich in Materialien (z. B. ausschließlich japanische Kondensatoren), Automatisierungsgrad (z. B. ausschließlich robotergestützte SMT-Produktionslinien) und Teststandards unterscheiden.