-
Edificio E, No. 65 Xingshan North Road, Liangtian, Parque Industrial Baisha, Distrito de Baiyun, Guangzhou
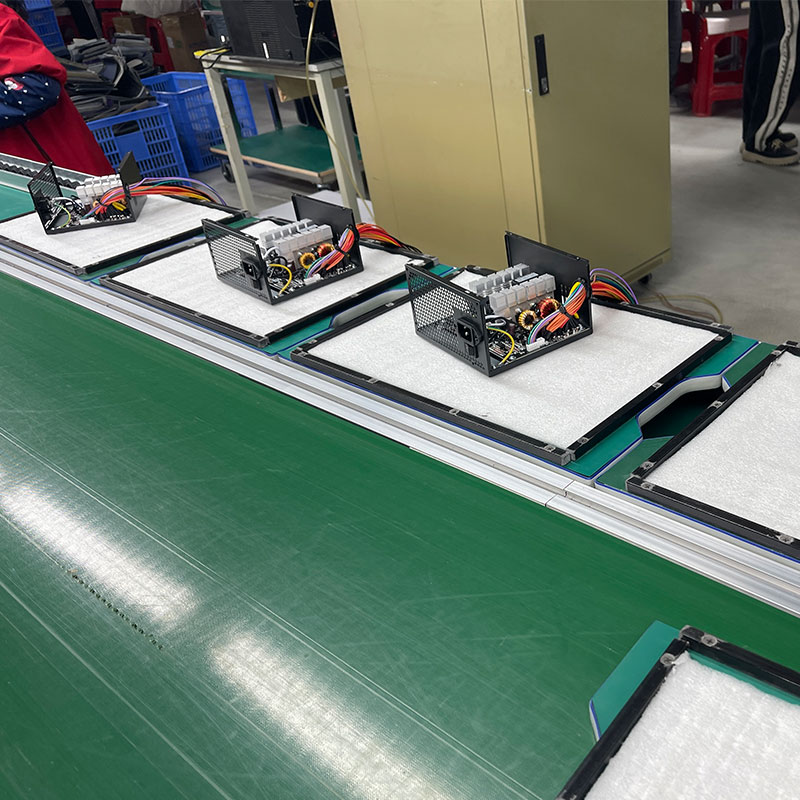
9 pasos para fabricar una fuente de alimentación de sobremesa
El proceso de producción de una fuente de alimentación de escritorio (unidad de fuente de alimentación para PC, PSU) involucra múltiples enlaces, que abarcan el ensamblaje de componentes electrónicos, el diseño de circuitos, las pruebas de seguridad, etc. A continuación, se presentan 9 pasos para producir una fuente de alimentación de sobremesa:
1. Diseño y desarrollo
Diseño del circuito:
El diseño y desarrollo de fuentes de alimentación de escritorio es el punto de partida del proceso de producción y determina directamente el rendimiento, la eficiencia y la confiabilidad del producto. En primer lugar, los ingenieros deben definir los parámetros de entrada y salida de la fuente de alimentación de acuerdo con los estándares de la industria (como las especificaciones Intel ATX), incluida la potencia nominal (como 500 W, 750 W), el rango de voltaje (+12 V, +5 V, +3,3 V, etc.) y el tipo de interfaz (fuente de alimentación de placa base de 24 pines, PCIe de 8 pines, etc.). El diseño del circuito central generalmente adopta la arquitectura de "PFC activo + resonancia LLC + rectificación sincrónica" para lograr una alta eficiencia de conversión (como la medalla de oro 80 PLUS o superior). En esta etapa, la estabilidad de la estructura de topología debe verificarse mediante un software de simulación (como SPICE) para garantizar que el voltaje pueda permanecer estable en condiciones extremas, como la mutación de carga y la alta temperatura.
Selección de componentes: seleccione componentes clave (como condensadores, inductores, MOSFET, transformadores, disipadores de calor, etc.), teniendo en cuenta la eficiencia (como la certificación 80 PLUS), la densidad de potencia y el costo.
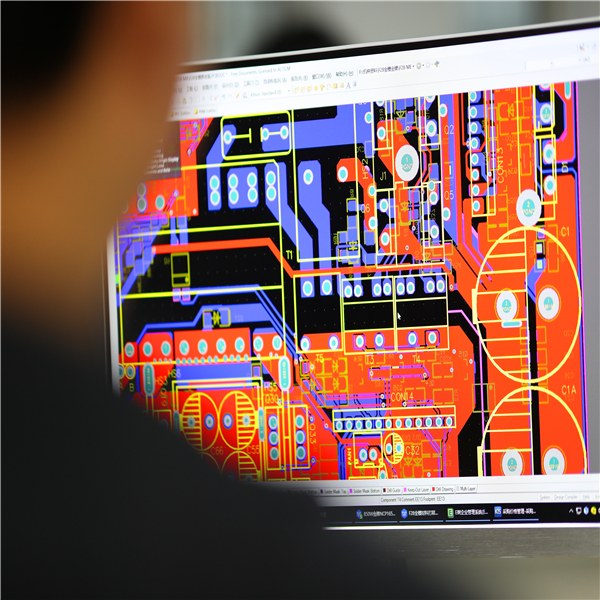
Verificación de simulación:
En cuanto a la selección de componentes, los componentes clave deben tener en cuenta tanto el rendimiento como el costo: el chip de control principal es en su mayoría soluciones taiwanesas (como Great Wall) o estadounidenses (como Texas Instruments); los condensadores deben cumplir con la resistencia a altas temperaturas (por encima de 105 °C) y una larga vida útil (como el japonés Nippon Chemi-Con); y los ventiladores de refrigeración deben equilibrar el ruido (<25 dB) y el volumen de aire. Además, el equipo de diseño debe optimizar el diseño de la PCB, como aislar el área de alto voltaje (lado primario) del área de bajo voltaje (lado secundario), reducir la interferencia electromagnética (EMI) y reducir la impedancia y la pérdida de calor a través del cableado multicapa.
Disposición de PCB:
La etapa de diseño también debe predecir los requisitos de certificación (como UL, CE, FCC) para evitar que la EMI supere el estándar o los riesgos de falla del aislamiento con anticipación. Por ejemplo, las distancias de seguridad (distancias de fuga y espacios libres eléctricos) deben cumplir con la norma IEC 60950, y el circuito PFC debe cumplir con los límites de armónicos IEC 61000-3-2. Finalmente, los documentos de diseño (incluidos los diagramas de circuitos, listas de materiales y modelos estructurales 3D) se transferirán a la etapa de producción para proporcionar una guía precisa para la posterior adquisición y ensamblaje de materiales. Este proceso generalmente demora entre varios meses y medio año y es la base de la calidad de la energía.
2. Adquisición e inspección de materias primas
La adquisición e inspección de materias primas son elementos cruciales en la producción de fuentes de alimentación para PC, que afectan directamente la calidad y la fiabilidad del producto. En cuanto a la adquisición de componentes, controlamos estrictamente la calidad de los componentes clave, como los condensadores electrolíticos, los inductores PFC, los transformadores principales, los chips de control de circuitos integrados y los ventiladores, que son el núcleo del rendimiento de las fuentes de alimentación. Las materias primas que compramos deben cumplir con las normas medioambientales RoHS para garantizar la protección del medio ambiente y la sostenibilidad de los productos.
La inspección de entrada de material (IQC) es la clave para garantizar que todos los componentes que entran en la línea de producción cumplan con los estándares de calidad. Realizamos inspecciones de calidad integrales de los componentes, incluida la capacidad y la tensión de resistencia de los condensadores, la resistencia de encendido de los MOSFET y otros parámetros clave para garantizar que cumplan plenamente con los requisitos de diseño. Nuestro proceso de IQC es riguroso y meticuloso, y cada lote de materias primas se prueba estrictamente para evitar que ingresen componentes no calificados al proceso de producción, lo que garantiza la excelente calidad y la confiabilidad a largo plazo del producto final. Esto nos ayuda a garantizar la calidad del producto y brindar mejores servicios.
3. Producción de PCB
La producción de PCB (placa de circuito impreso) es el eslabón principal de la fabricación de fuentes de alimentación para PC. Proporciona una conexión y un soporte fiables para los componentes electrónicos, al igual que el "esqueleto" de la fuente de alimentación. Nuestro proceso de producción de PCB sigue estrictamente los estándares de la industria para garantizar que cada PCB tenga un rendimiento y una durabilidad excelentes.
Producción de sustrato:
Seleccionamos sustratos aislantes de alta calidad, como FR-4 o materiales de grado superior, que tienen excelentes propiedades de aislamiento eléctrico y resistencia mecánica. Se lamina una lámina de cobre al sustrato aislante para formar un sustrato de PCB. El espesor de la lámina de cobre suele estar entre 1 onza (aproximadamente 35 micrones) o 2 onzas (aproximadamente 70 micrones), y la elección específica depende del nivel de corriente y voltaje de diseño de la fuente de alimentación.
Fotolitografía y grabado:
Utilizamos la fotolitografía para transferir el patrón del circuito al sustrato de la placa de circuito impreso. Esto es similar al proceso de revelado de una fotografía, en el que el material fotosensible se expone de acuerdo con el diagrama del circuito. A través del grabado, eliminamos el exceso de capa de cobre, dejando las pistas y almohadillas del circuito necesarias, formando así el sistema de "vasos sanguíneos" de la fuente de alimentación. La precisión del grabado suele alcanzar los 0,1 mm o menos para satisfacer las necesidades del diseño de circuitos de alta densidad.
Perforación y deposición de cobre:
Es un paso clave en la producción de PCB. Utilizamos equipos de perforación de alta precisión para perforar orificios pasantes (vías) y orificios para pasadores de componentes en PCB. Los orificios pasantes se utilizan para conectar diferentes capas de PCB y proporcionar canales para la transmisión de corriente. El proceso de recubrimiento de cobre consiste en recubrir una capa de cobre en la pared del orificio perforado para garantizar la conductividad del orificio pasante. El control del tamaño y el espaciado de los orificios es crucial para el rendimiento eléctrico de la PCB. Por ejemplo, el diámetro del orificio pasante suele estar entre 0,3 mm y 0,6 mm para satisfacer las necesidades de transmisión de corriente.
Máscara de soldadura y serigrafía:
Aplicamos tinta de máscara de soldadura, generalmente verde u otros colores, sobre la superficie de la PCB para proteger las trazas del circuito de la corrosión y los cortocircuitos. La máscara de soldadura también se utiliza para delimitar el área de soldadura del componente. A continuación, imprimimos la identificación del componente en la PCB, como el número de resistencias y condensadores, para facilitar el posterior montaje y mantenimiento del componente. El espesor de la máscara de soldadura suele estar entre 15 micras y 30 micras para garantizar una buena protección del circuito. Después de estos rigurosos procesos, cada PCB alcanzará un rendimiento óptimo.
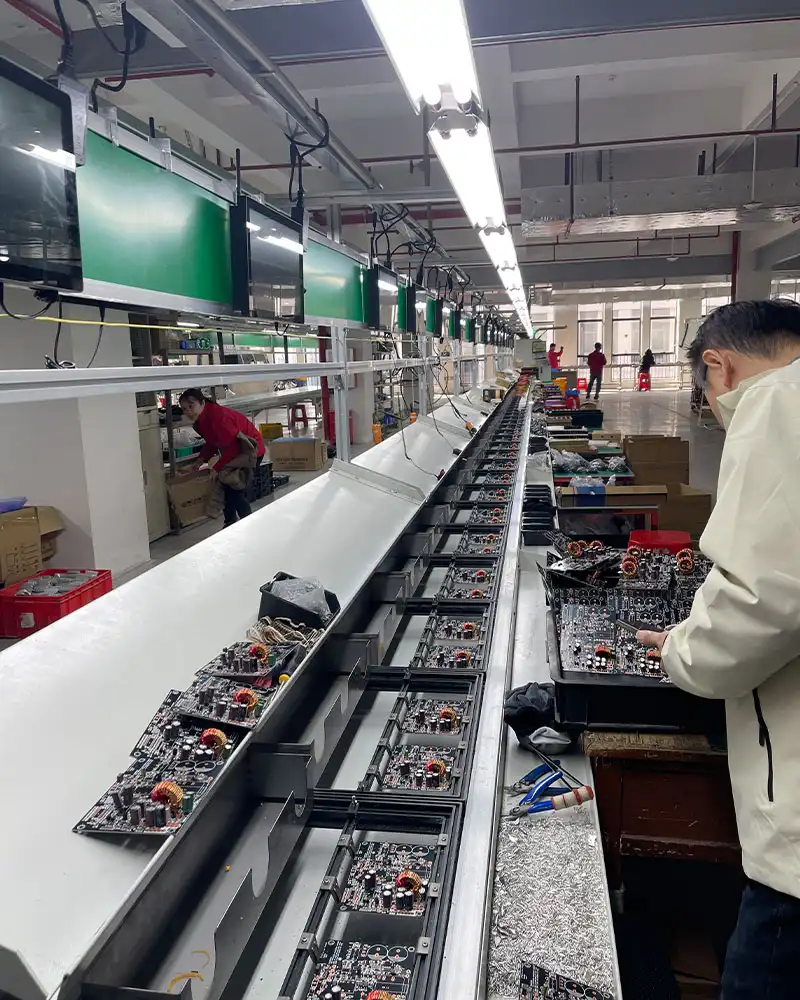
4. Instalación de componentes
Es un paso clave en el montaje de la fuente de alimentación de PC. Conecta el “esqueleto” de la PCB con varios componentes electrónicos para formar el “corazón” de la fuente de alimentación. Nuestro proceso de instalación de componentes utiliza tecnología SMT (montaje superficial) avanzada y tecnología de conexión tradicional para garantizar una instalación precisa y una conexión confiable de los componentes.
Parche SMT:
Con la ayuda de máquinas de parcheo de alta precisión, soldamos con precisión pequeños componentes como resistencias, condensadores, chips IC, etc. a las almohadillas de la PCB. La máquina de parcheo puede lograr un parcheo de alta velocidad y alta precisión, y la precisión del parche generalmente puede alcanzar 0,1 mm. Luego, utilizamos el proceso de soldadura por reflujo para fundir la pasta de soldadura de modo que los componentes queden firmemente fijados en la PCB. La curva de temperatura de la soldadura por reflujo se controla con precisión para garantizar la calidad de la soldadura.
Instalación de componentes:
Se utiliza para componentes de gran tamaño, como condensadores electrolíticos, transformadores y pines de disipadores de calor. Estos componentes suelen ser de gran tamaño y no se pueden reparar mediante SMT. Nuestros trabajadores insertan estos componentes en los orificios correspondientes de la PCB de forma manual o a máquina durante el proceso de inserción. La inserción manual garantiza la flexibilidad y precisión de la instalación, mientras que la inserción a máquina mejora la eficiencia y la consistencia.
Soldadura por ola:
Soldadura de componentes enchufables para formar conexiones eléctricas confiables. La soldadura por ola consiste en sumergir la PCB en soldadura fundida para que la soldadura humedezca los pines del componente y forme uniones de soldadura. La temperatura y el tiempo de soldadura por ola se controlan con precisión para garantizar la calidad de la soldadura. A través de estos rigurosos procesos, cada fuente de alimentación se ensambla para lograr un rendimiento óptimo.
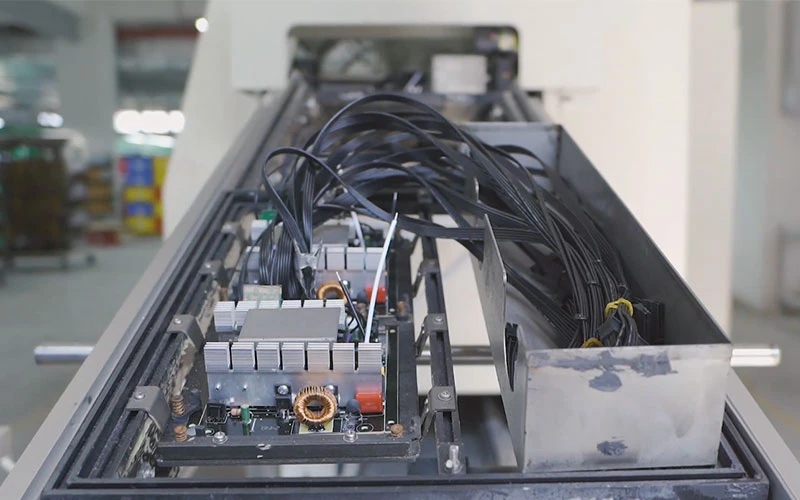
5. Conjunto del módulo de llave
Es el eslabón central de la fabricación de fuentes de alimentación para PC. Estos módulos determinan directamente el rendimiento, la eficiencia y la confiabilidad de la fuente de alimentación. Utilizamos procesos precisos y un estricto control de calidad en el ensamblaje de módulos clave para garantizar que cada módulo pueda lograr un rendimiento óptimo.
Módulo PFC (corrección del factor de potencia):
Instalaremos circuitos de corrección del factor de potencia activos o pasivos para mejorar el uso de la energía. Los circuitos de corrección del factor de potencia activos pueden mejorar significativamente el factor de potencia de la fuente de alimentación hasta cerca de 1, reduciendo así las pérdidas de potencia reactiva en la red eléctrica y cumpliendo con los estándares de eficiencia energética. Garantizaremos la calidad y la instalación de componentes clave como los inductores de corrección del factor de potencia para garantizar el rendimiento de los módulos de corrección del factor de potencia.
Módulo transformador y rectificador principal:
Montaremos transformadores de alta frecuencia para aislar la corriente alterna y ajustar el voltaje. La calidad y el diseño del transformador son cruciales para la eficiencia y la estabilidad de la fuente de alimentación. Al mismo tiempo, también montaremos circuitos de rectificación, como rectificación síncrona o diodos Schottky. Estos componentes se utilizan para convertir la corriente alterna en corriente continua para proporcionar el voltaje necesario para varios componentes de la computadora. La selección e instalación correctas de estos componentes son cruciales para la calidad de salida de la fuente de alimentación.
Sistema de enfriamiento:
Dado que la fuente de alimentación genera calor durante su funcionamiento, el sistema de refrigeración es crucial. Fijaremos el disipador de calor, normalmente fabricado con aleación de aluminio, para aumentar el área de disipación de calor. También aplicaremos silicona termoconductora para mejorar la conducción de calor entre el disipador de calor y el elemento calefactor. Además, instalaremos un ventilador de refrigeración, normalmente un ventilador de 12 cm o 14 cm, para proporcionar una circulación de aire eficaz, eliminar el calor del interior de la fuente de alimentación y mantener la fuente de alimentación funcionando de forma estable.
6. Conjunto del módulo de potencia
Es el último proceso de fabricación de fuentes de alimentación para PC, que integra todos los componentes internos para formar una fuente de alimentación completa y utilizable. En este enlace, prestamos atención a cada detalle para garantizar la seguridad, la estabilidad y la belleza de la fuente de alimentación.
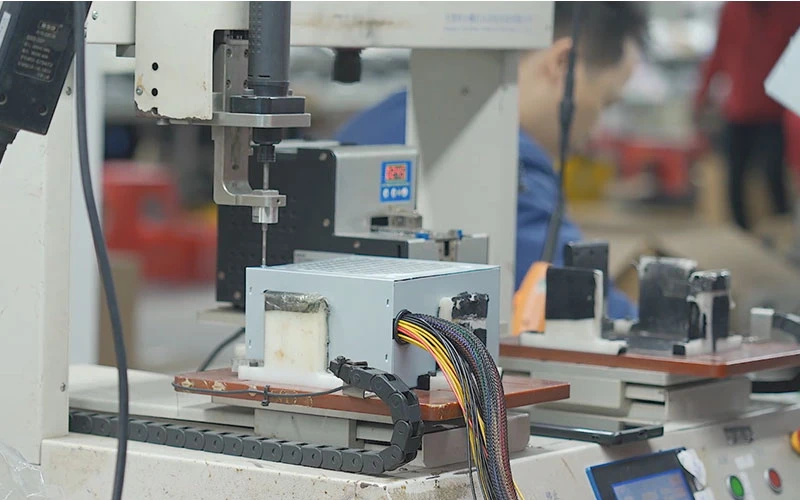
Conjunto de carcasa:
Instalamos componentes internos como PCB (placa de circuito impreso), ventilador, interruptor, etc. en la carcasa de metal, que generalmente está hecha de placa de acero galvanizado para brindar una protección sólida y un buen efecto de blindaje EMI (interferencia electromagnética). El blindaje EMI puede prevenir eficazmente que la radiación electromagnética dentro de la fuente de alimentación interfiera con otros dispositivos electrónicos y reducir el impacto de la interferencia electromagnética externa en la fuente de alimentación. Durante el proceso de ensamblaje de la carcasa, nos aseguramos de que todos los componentes estén firmemente fijados en la carcasa y firmemente conectados a la carcasa.
Soldadura de cable:
Conectaremos varios cables de salida, incluida la fuente de alimentación de la placa base de 24 pines, la fuente de alimentación PCIe, la fuente de alimentación SATA, etc., que se utilizan para proporcionar energía a varios componentes de la computadora. La calidad de la soldadura está directamente relacionada con la estabilidad y confiabilidad de la fuente de alimentación. Utilizamos materiales y procesos de soldadura de alta calidad para garantizar que los puntos de soldadura sean firmes y confiables. Después de la soldadura, colocaremos fundas aislantes en los cables para evitar cortocircuitos y otros peligros de seguridad.
Fijación y aislamiento:
Utilizamos tornillos para fijar los componentes internos para evitar que se muevan o se aflojen durante el transporte o el uso. Para mejorar aún más la seguridad de la fuente de alimentación, también agregamos láminas aislantes o almohadillas de goma para evitar cortocircuitos entre los componentes internos. El material y el grosor de la lámina aislante se seleccionan cuidadosamente para garantizar un buen aislamiento. A través de estos procesos, cada módulo de potencia logrará un efecto seguro, estable y confiable.
7. Pruebas y calibración
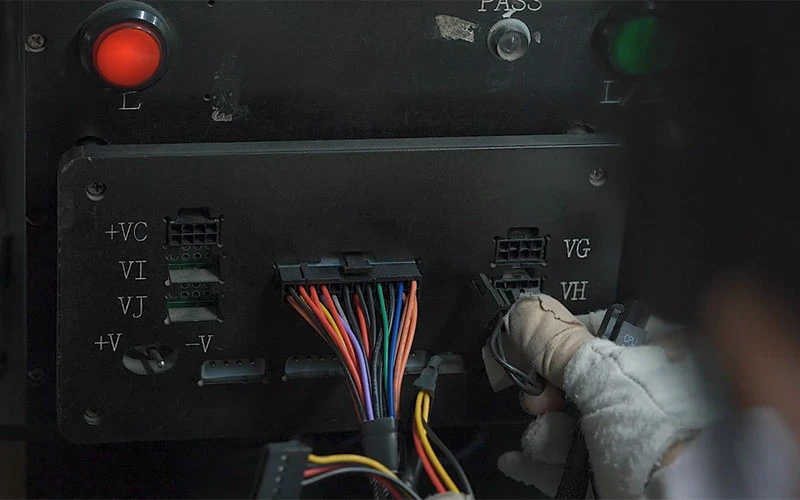
Prueba de encendido:
Verifique si el voltaje sin carga y la fuente de alimentación de reserva (+5VSB) son normales.
Prueba de carga: simula el funcionamiento a plena carga para verificar la estabilidad de cada salida de voltaje (+12 V, +5 V, +3,3 V).
Prueba de función de protección:
activa la protección contra sobretensión (OVP), la protección contra sobrecorriente (OCP), la protección contra cortocircuitos (SCP), etc.
Prueba de eficiencia y ondulación:
medir la eficiencia de conversión (como los requisitos de certificación 80 PLUS) y la ondulación de salida (debe cumplir con los estándares Intel ATX).
Prueba de quemado: se ejecuta de forma continua durante varias horas para detectar componentes con fallas tempranas.
8. Certificación e inspección de conformidad
Certificación de seguridad: pasa UL, CE, FCC, CCC y otras certificaciones para garantizar el cumplimiento de los estándares de seguridad regionales.
Certificación de eficiencia energética: solicita la certificación 80 PLUS (bronce/oro/titanio, etc.) y marca el nivel de eficiencia.
Prueba EMI/EMC: garantiza que la radiación electromagnética cumpla con las regulaciones para evitar interferencias con otros dispositivos.
9. Embalaje y envío
Inspección de apariencia: limpie la carcasa y verifique que no tenga rayones ni defectos de montaje.
Embalaje de accesorios: se incluyen cable de alimentación, tornillos, manual, etc.
Código de barras y trazabilidad: Se adjunta una etiqueta con el número de serie SN para facilitar la trazabilidad de la calidad.
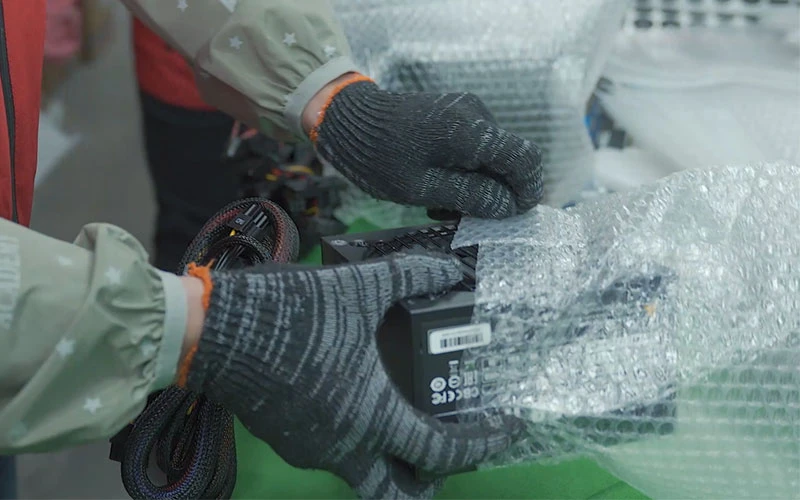
Puntos clave de control de calidad
Los pasos anteriores son los 9 para fabricar una fuente de alimentación de sobremesa. Además, hay que tener en cuenta los siguientes puntos:
Vida útil del condensador: seleccione condensadores japoneses o taiwaneses de alta calidad (como Rubycon, Nippon Chemi-Con).
Diseño de disipación de calor: equilibra la velocidad del ventilador y el ruido para garantizar un control de temperatura a largo plazo.
Calidad de la soldadura: Evite el mal contacto causado por soldaduras falsas y soldaduras en frío.
Tendencias de la industria
Miniaturización y alta densidad de potencia: por ejemplo, la fuente de alimentación SFX se adapta a un host pequeño.
Control digital: Utilice un procesador de señal digital (DSP) para lograr una regulación de voltaje inteligente.
Diseño totalmente modular: los usuarios pueden personalizar los cables para reducir el desorden en el chasis.
A través del proceso mencionado anteriormente, las fuentes de alimentación de escritorio deben someterse a un estricto control y pruebas desde el diseño hasta el producto terminado para garantizar su confiabilidad, eficiencia y seguridad. Las diferentes marcas pueden diferir en los materiales (como los condensadores totalmente japoneses), el grado de automatización (como las líneas de producción SMT totalmente robotizadas) y los estándares de prueba.