-
ساختمان E، شماره 65 جاده Xingshan شمالی، لیانگتیان، پارک صنعتی بایشا، منطقه بایون، گوانگژو
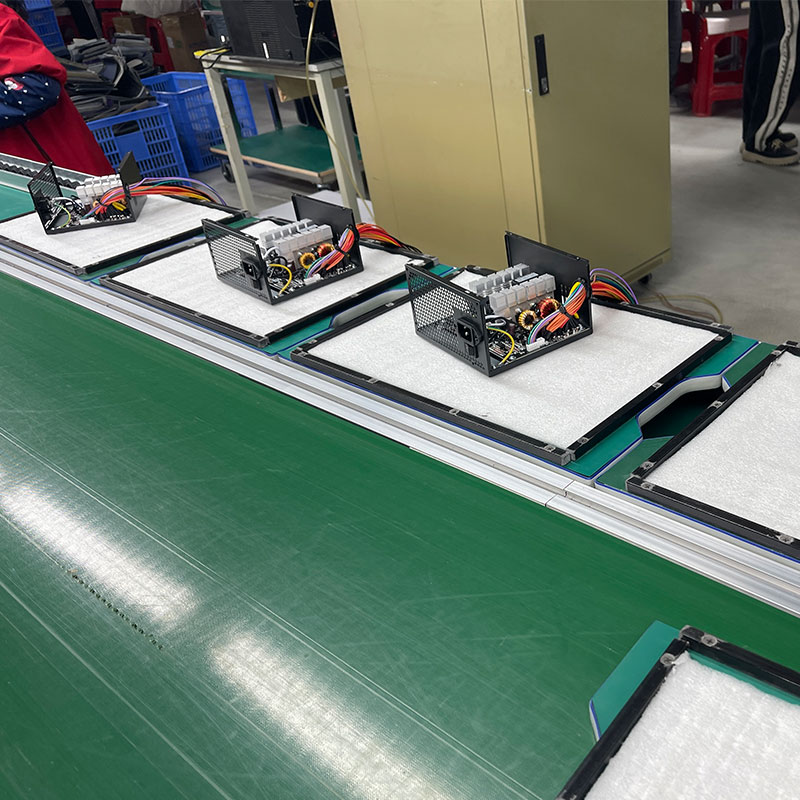
9 مرحله برای تولید یک منبع تغذیه میز
فرآیند تولید یک منبع تغذیه رومیزی (واحد منبع تغذیه رایانه شخصی، PSU) شامل پیوندهای متعدد، پوشش مونتاژ قطعات الکترونیکی، طراحی مدار، تست ایمنی و غیره است. در زیر 9 مرحله برای تولید منبع تغذیه رومیزی آورده شده است:
1. طراحی و توسعه
طراحی مدار:
طراحی و توسعه منابع تغذیه رومیزی نقطه شروع فرآیند تولید است و به طور مستقیم عملکرد، کارایی و قابلیت اطمینان محصول را تعیین می کند. ابتدا مهندسان باید پارامترهای ورودی و خروجی منبع تغذیه را بر اساس استانداردهای صنعت (مانند مشخصات ATX اینتل)، از جمله توان نامی (مانند 500 وات، 750 وات)، محدوده ولتاژ (+12 ولت، + 5 ولت، + 3.3 ولت و غیره) و نوع رابط (منبع تغذیه 8 پین مادربرد 24 پین، PCIe و غیره) تعریف کنند. طراحی مدار اصلی معمولاً از معماری "PFC+LLC فعال رزونانس + تصحیح همزمان" برای دستیابی به راندمان تبدیل بالا (مانند مدال طلای 80 PLUS یا بالاتر) استفاده می کند. در این مرحله، پایداری ساختار توپولوژی باید از طریق نرمافزار شبیهسازی (مانند SPICE) تأیید شود تا اطمینان حاصل شود که ولتاژ میتواند در شرایط شدید مانند جهش بار و دمای بالا پایدار بماند.
انتخاب کامپوننت: اجزای کلیدی (مانند خازن ها، سلف ها، ماسفت ها، ترانسفورماتورها، هیت سینک ها و غیره) را با در نظر گرفتن کارایی (مانند گواهینامه 80 PLUS)، چگالی توان و هزینه انتخاب کنید.
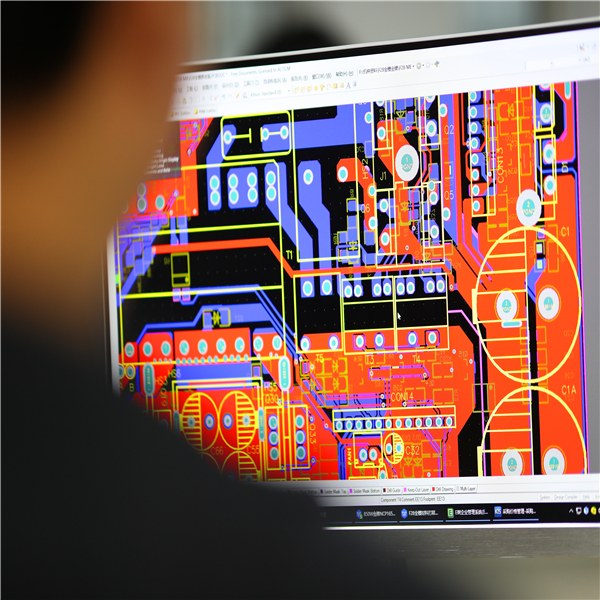
تایید شبیه سازی:
از نظر انتخاب جزء، اجزای کلیدی باید هم کارایی و هم هزینه را در نظر بگیرند: تراشه کنترل اصلی عمدتاً راه حل های تایوانی (مانند Great Wall) یا آمریکایی (مانند Texas Instruments) است. خازن ها نیاز به مقاومت در برابر دمای بالا (بالای 105 درجه سانتیگراد) و عمر طولانی (مانند ژاپنی Nippon Chemi-Con) دارند. و فن های خنک کننده باید صدا (<25dB) و حجم هوا را متعادل کنند. علاوه بر این، تیم طراحی نیاز به بهینه سازی طرح PCB دارد، مانند جداسازی ناحیه ولتاژ بالا (سمت اصلی) از ناحیه ولتاژ پایین (سمت ثانویه)، کاهش تداخل الکترومغناطیسی (EMI) و کاهش امپدانس و اتلاف حرارت از طریق سیم کشی چند لایه.
طرح PCB:
مرحله طراحی همچنین نیاز به پیشبینی الزامات گواهینامه (مانند UL، CE، FCC) دارد تا EMI از حد استاندارد یا خطرات شکست عایق جلوگیری کند. به عنوان مثال، فواصل ایمنی (فاصله خزش و فاصله های الکتریکی) باید با استاندارد IEC 60950 مطابقت داشته باشد و مدار PFC باید محدودیت های هارمونیک IEC 61000-3-2 را داشته باشد. در نهایت، اسناد طراحی (شامل نمودارهای مدار، لیستهای BOM و مدلهای ساختاری سهبعدی) به مرحله تولید منتقل میشوند تا راهنمایی دقیق برای تهیه و مونتاژ مواد بعدی ارائه شود. این فرآیند معمولا از چند ماه تا نیم سال طول می کشد و پایه و اساس کیفیت برق است.
2. تهیه و بازرسی مواد خام
تهیه و بازرسی مواد خام، پیوندهای حیاتی در تولید منبع تغذیه رایانه شخصی است که مستقیماً بر کیفیت و قابلیت اطمینان محصول تأثیر می گذارد. از نظر تهیه قطعات، ما کیفیت قطعات کلیدی مانند خازن های الکترولیتی، سلف های PFC، ترانسفورماتورهای اصلی، تراشه های کنترل آی سی و فن ها را که هسته اصلی عملکرد منبع تغذیه هستند، به شدت کنترل می کنیم. مواد اولیه ای که ما خریداری می کنیم باید با استانداردهای زیست محیطی RoHS مطابقت داشته باشد تا از حفاظت از محیط زیست و پایداری محصولات اطمینان حاصل شود.
بازرسی مواد ورودی (IQC) کلیدی است برای اطمینان از اینکه تمام قطعات وارد خط تولید با استانداردهای کیفیت مطابقت دارند. ما بازرسی های کیفیت جامعی را روی قطعات انجام می دهیم، از جمله ظرفیت و ولتاژ مقاومت خازن ها، مقاومت در برابر ماسفت ها و سایر پارامترهای کلیدی تا اطمینان حاصل کنیم که آنها به طور کامل الزامات طراحی را برآورده می کنند. فرآیند IQC ما دقیق و دقیق است و هر دسته از مواد خام به شدت آزمایش می شود تا از ورود هر گونه اجزای فاقد صلاحیت به فرآیند تولید جلوگیری شود و در نتیجه کیفیت عالی و قابلیت اطمینان طولانی مدت محصول نهایی تضمین شود. این به ما کمک می کند تا کیفیت محصول را تضمین کنیم و خدمات بهتری ارائه دهیم.
3. تولید PCB
تولید PCB (برد مدار چاپی) پیوند اصلی تولید منبع تغذیه رایانه شخصی است. این اتصال و پشتیبانی قابل اعتماد برای قطعات الکترونیکی، درست مانند "اسکلت" منبع تغذیه فراهم می کند. فرآیند تولید PCB ما به شدت از استانداردهای صنعت پیروی می کند تا اطمینان حاصل شود که هر PCB دارای عملکرد و دوام عالی است.
تولید بستر:
ما زیرلایه های عایق با کیفیت بالا مانند مواد FR-4 یا درجه بالاتر را انتخاب می کنیم که خواص عایق الکتریکی و استحکام مکانیکی عالی دارند. فویل مسی روی بستر عایق لمینت می شود تا یک بستر PCB تشکیل شود. ضخامت فویل مس معمولاً بین 1 اونس (حدود 35 میکرون) یا 2 اونس (حدود 70 میکرون) است و انتخاب خاص بستگی به جریان طراحی و سطح ولتاژ منبع تغذیه دارد.
فتولیتوگرافی و اچینگ:
ما از فوتولیتوگرافی برای انتقال الگوی مدار به بستر PCB استفاده می کنیم. این شبیه به فرآیند ایجاد یک عکس است که در آن مواد حساس به نور طبق نمودار مدار در معرض دید قرار می گیرند. از طریق اچ کردن، لایه مس اضافی را حذف می کنیم و آثار مدار و پدهای مورد نیاز را باقی می گذاریم و در نتیجه سیستم "رگ خونی" منبع تغذیه را تشکیل می دهیم. دقت اچ معمولاً می تواند به 0.1 میلی متر یا کمتر برسد تا نیازهای طراحی مدار با چگالی بالا را برآورده کند.
حفاری و رسوب مس:
این یک مرحله کلیدی در تولید PCB است. ما از تجهیزات حفاری با دقت بالا برای سوراخ کردن سوراخها (ویاس) و سوراخهای پین اجزا بر روی PCB استفاده میکنیم. سوراخهای عبوری برای اتصال لایههای مختلف PCB و ارائه کانالهایی برای انتقال جریان استفاده میشوند. فرآیند آبکاری مس به این صورت است که لایه ای از مس را بر روی دیواره سوراخ حفر شده قرار می دهند تا از هدایت سوراخ عبور اطمینان حاصل شود. کنترل اندازه سوراخ و فاصله برای عملکرد الکتریکی PCB بسیار مهم است. به عنوان مثال، قطر سوراخ عبوری معمولاً بین 0.3 میلی متر تا 0.6 میلی متر است تا نیازهای انتقال جریان را برآورده کند.
ماسک لحیم کاری و صفحه ابریشم:
ما جوهر ماسک لحیم کاری، معمولاً سبز یا رنگ های دیگر را روی سطح PCB اعمال می کنیم تا آثار مدار را از خوردگی و اتصال کوتاه محافظت کند. از ماسک لحیم کاری نیز برای تعیین ناحیه لحیم کاری قطعه استفاده می شود. در مرحله بعد، شناسایی اجزا را روی PCB چاپ می کنیم، مانند تعداد مقاومت ها و خازن ها، تا مونتاژ و نگهداری قطعات بعدی را تسهیل کنیم. ضخامت ماسک لحیم کاری به طور کلی بین 15 میکرون تا 30 میکرون است تا از حفاظت خوب مدار اطمینان حاصل شود. پس از این فرآیندهای سخت، هر PCB به عملکرد مطلوب دست خواهد یافت.
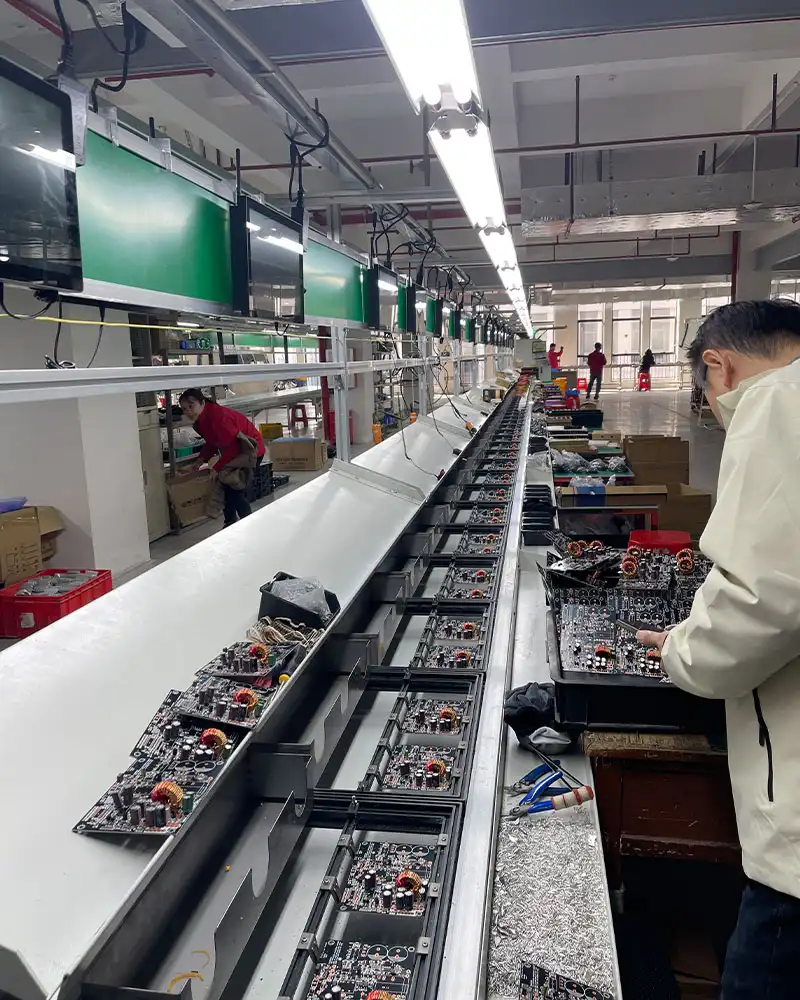
4. نصب کامپوننت
این یک مرحله کلیدی در مونتاژ منبع تغذیه رایانه شخصی است. "اسکلت" روی PCB را با قطعات الکترونیکی مختلف متصل می کند تا "قلب" منبع تغذیه را تشکیل دهد. فرآیند نصب قطعات ما از SMT پیشرفته (فناوری نصب سطحی) و فناوری سنتی پلاگین برای اطمینان از نصب دقیق و اتصال مطمئن قطعات استفاده می کند.
پچ SMT:
با کمک دستگاه های پچ با دقت بالا، قطعات کوچک مانند مقاومت ها، خازن ها، تراشه های آی سی و غیره را به دقت به لنت های PCB لحیم می کنیم. دستگاه پچ می تواند به وصله با سرعت و دقت بالا دست یابد و دقت پچ معمولاً می تواند به 0.1 میلی متر برسد. سپس از فرآیند لحیم کاری مجدد برای ذوب خمیر لحیم استفاده می کنیم تا اجزا به طور محکم روی PCB ثابت شوند. منحنی دمای لحیم کاری مجدد دقیقاً کنترل می شود تا از کیفیت جوش اطمینان حاصل شود.
نصب کامپوننت:
این برای قطعات با اندازه بزرگ مانند خازن های الکترولیتی، ترانسفورماتورها و پین های هیت سینک است. این کامپوننت ها معمولاً اندازه بزرگی دارند و نمی توانند توسط SMT وصله شوند. کارگران ما این قطعات را در حفره های مربوطه PCB به صورت دستی یا توسط ماشین در طی فرآیند پلاگین وارد می کنند. پلاگین دستی انعطاف پذیری و دقت نصب را تضمین می کند، در حالی که پلاگین ماشین کارایی و سازگاری را بهبود می بخشد.
لحیم کاری موجی:
لحیم کاری قطعات پلاگین برای ایجاد اتصالات الکتریکی قابل اعتماد. لحیم کاری موجی عبارت است از فرو بردن PCB در لحیم مذاب به طوری که لحیم پین های اجزا را خیس کرده و اتصالات لحیم ایجاد کند. دما و زمان لحیم کاری موج دقیقاً کنترل می شود تا از کیفیت لحیم کاری اطمینان حاصل شود. از طریق این فرآیندهای دقیق، هر منبع تغذیه برای عملکرد بهینه مونتاژ می شود.
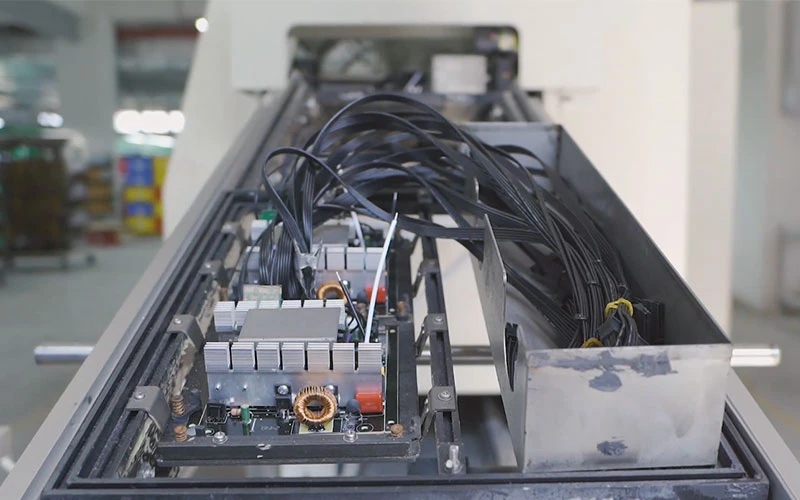
5. مونتاژ ماژول کلید
این حلقه اصلی تولید منبع تغذیه رایانه شخصی است. این ماژول ها به طور مستقیم عملکرد، کارایی و قابلیت اطمینان منبع تغذیه را تعیین می کنند. ما از فرآیندهای دقیق و کنترل کیفیت دقیق در مونتاژ ماژول های کلیدی استفاده می کنیم تا اطمینان حاصل کنیم که هر ماژول می تواند به عملکرد مطلوب دست یابد.
ماژول PFC (تصحیح ضریب توان):
ما مدارهای تصحیح ضریب توان فعال یا غیرفعال را برای بهبود مصرف برق نصب خواهیم کرد. مدارهای فعال PFC می توانند به طور قابل توجهی ضریب توان منبع تغذیه را نزدیک به 1 بهبود بخشند و در نتیجه تلفات توان راکتیو در شبکه برق را کاهش دهند و استانداردهای بهره وری انرژی را برآورده کنند. ما کیفیت و نصب اجزای کلیدی مانند سلف های PFC را برای اطمینان از عملکرد ماژول های PFC تضمین خواهیم کرد.
ترانسفورماتور اصلی و ماژول یکسو کننده:
ما ترانسفورماتورهای فرکانس بالا را برای جداسازی برق متناوب و تنظیم ولتاژ جمع می کنیم. کیفیت و طراحی ترانسفورماتور برای کارایی و پایداری منبع تغذیه بسیار مهم است. در همان زمان، ما مدارهای یکسوسازی مانند یکسوسازی سنکرون یا دیودهای شاتکی را نیز مونتاژ خواهیم کرد. از این قطعات برای تبدیل برق متناوب به برق DC برای تامین ولتاژ مورد نیاز برای اجزای مختلف کامپیوتر استفاده می شود. انتخاب و نصب صحیح این قطعات برای کیفیت خروجی منبع تغذیه بسیار مهم است.
سیستم خنک کننده:
از آنجایی که منبع تغذیه در حین کار گرما تولید می کند، سیستم خنک کننده بسیار مهم است. ما سینک حرارتی را که معمولاً از آلیاژ آلومینیوم ساخته شده است، تعمیر می کنیم تا ناحیه اتلاف گرما را افزایش دهیم. ما همچنین از سیلیکون رسانای حرارتی برای افزایش رسانش گرما بین هیت سینک و المنت حرارتی استفاده می کنیم. علاوه بر این، ما یک فن خنک کننده، معمولاً یک فن 12 سانتی متری یا 14 سانتی متری را نصب می کنیم تا گردش هوای موثری داشته باشیم، گرما را از داخل منبع تغذیه حذف کنیم و منبع تغذیه را به طور پایدار نگه داریم.
6. مونتاژ ماژول برق
این آخرین فرآیند تولید منبع تغذیه رایانه شخصی است که تمام اجزای داخلی را با هم ادغام می کند تا یک منبع تغذیه کامل و قابل استفاده را تشکیل دهد. در این لینک برای اطمینان از ایمنی، پایداری و زیبایی منبع تغذیه به تمام جزئیات توجه می کنیم.
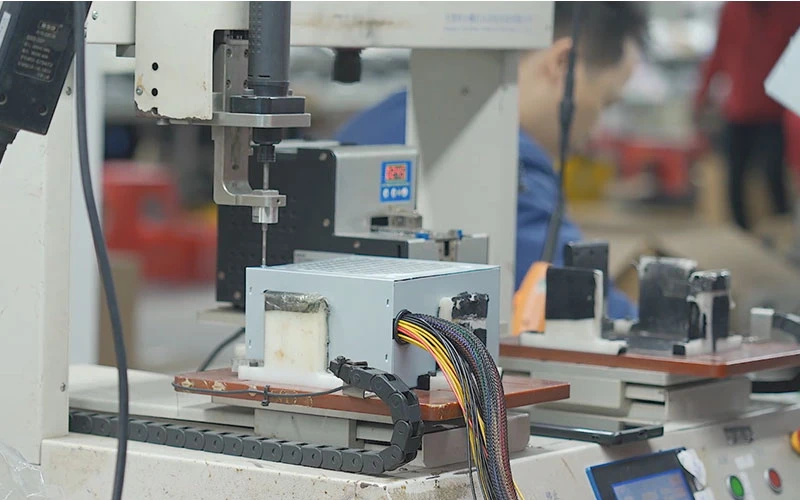
مونتاژ بدنه:
ما قطعات داخلی مانند PCB (برد مدار چاپی)، فن، سوئیچ و غیره را در محفظه فلزی نصب میکنیم که معمولاً از ورق فولادی گالوانیزه ساخته میشود تا محافظت جامد و اثر محافظتی خوب EMI (تداخل الکترومغناطیسی) داشته باشد. محافظ EMI می تواند به طور موثری از تداخل تابش الکترومغناطیسی داخل منبع تغذیه با سایر دستگاه های الکترونیکی جلوگیری کند و تأثیر تداخل الکترومغناطیسی خارجی بر منبع تغذیه را کاهش دهد. در طول فرآیند مونتاژ پوشش، ما اطمینان حاصل می کنیم که تمام اجزا به طور محکم در پوشش ثابت شده و محکم به بدنه متصل شده اند.
جوش کابل:
ما کابل های خروجی مختلفی از جمله منبع تغذیه مادربرد 24 پین، منبع تغذیه PCIe، منبع تغذیه SATA و غیره را به هم وصل خواهیم کرد که برای تامین برق اجزای مختلف کامپیوتر استفاده می شود. کیفیت جوش ارتباط مستقیمی با پایداری و قابلیت اطمینان منبع تغذیه دارد. ما از مواد و فرآیندهای جوشکاری با کیفیت بالا استفاده می کنیم تا اطمینان حاصل کنیم که نقاط جوش محکم و قابل اعتماد هستند. پس از جوشکاری، برای جلوگیری از اتصال کوتاه و سایر خطرات ایمنی، روی کابل ها آستین های عایق قرار می دهیم.
تعمیر و عایق کاری:
ما از پیچ برای تعمیر قطعات داخلی استفاده می کنیم تا از جابجایی یا شل شدن آنها در حین حمل و نقل یا استفاده جلوگیری کنیم. برای بهبود بیشتر ایمنی منبع تغذیه، ورق های عایق یا لنت های لاستیکی را نیز اضافه می کنیم تا از اتصال کوتاه بین اجزای داخلی جلوگیری کنیم. مواد و ضخامت ورق عایق با دقت انتخاب می شوند تا از عایق خوب اطمینان حاصل شود. از طریق این فرآیندها، هر ماژول قدرت به یک اثر ایمن، پایدار و قابل اعتماد دست خواهد یافت.
7. تست و کالیبراسیون
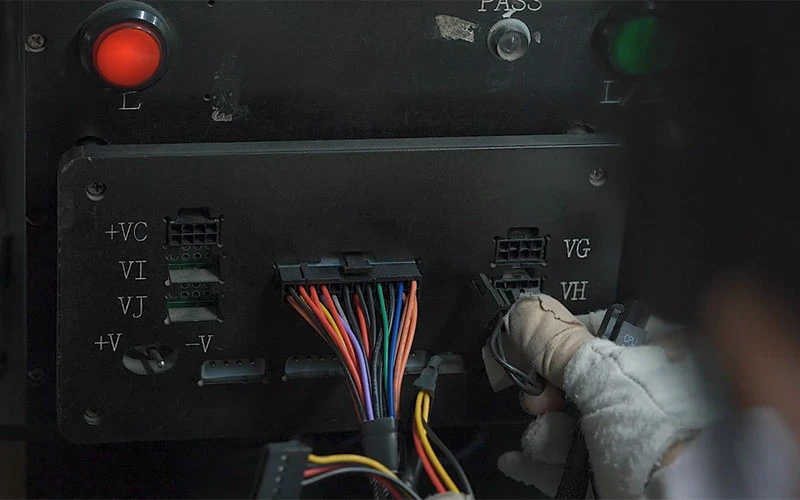
تست روشن شدن:
بررسی کنید که آیا ولتاژ بدون بار و منبع تغذیه آماده به کار (+5VSB) طبیعی است یا خیر.
تست بار: شبیه سازی عملیات بار کامل برای بررسی پایداری هر خروجی ولتاژ (+12V، +5V، +3.3V).
تست عملکرد حفاظتی:
حفاظت از اضافه ولتاژ ماشه (OVP)، حفاظت از جریان اضافه (OCP)، حفاظت از اتصال کوتاه (SCP) و غیره.
تست کارایی و ریپل:
راندمان تبدیل (مانند الزامات گواهینامه 80 PLUS) و ریپل خروجی را اندازه گیری کنید (باید با استانداردهای ATX اینتل مطابقت داشته باشد).
تست Burn-in: برای چند ساعت به طور مداوم اجرا کنید تا اجزای خطای اولیه را بررسی کنید.
8. صدور گواهینامه و بازرسی انطباق
گواهینامه ایمنی: گواهینامه های UL، CE، FCC، CCC و سایر گواهینامه ها را برای اطمینان از انطباق با استانداردهای ایمنی منطقه ای پاس کنید.
گواهینامه بهره وری انرژی: برای گواهینامه 80 PLUS (برنز/طلا/تیتانیوم و غیره) درخواست دهید و سطح کارایی را علامت بزنید.
تست EMI/EMC: اطمینان حاصل کنید که تشعشعات الکترومغناطیسی با مقررات مطابقت دارد تا از تداخل با سایر دستگاه ها جلوگیری شود.
9. بسته بندی و حمل و نقل
بازرسی ظاهری: پوشش را تمیز کنید و خراش یا نقص مونتاژ را بررسی کنید.
بسته بندی لوازم جانبی: سیم برق، پیچ، دفترچه راهنما و غیره گنجانده شده است.
بارکد و قابلیت ردیابی: برچسب شماره سریال SN برای ردیابی آسان با کیفیت چسبانده شده است.
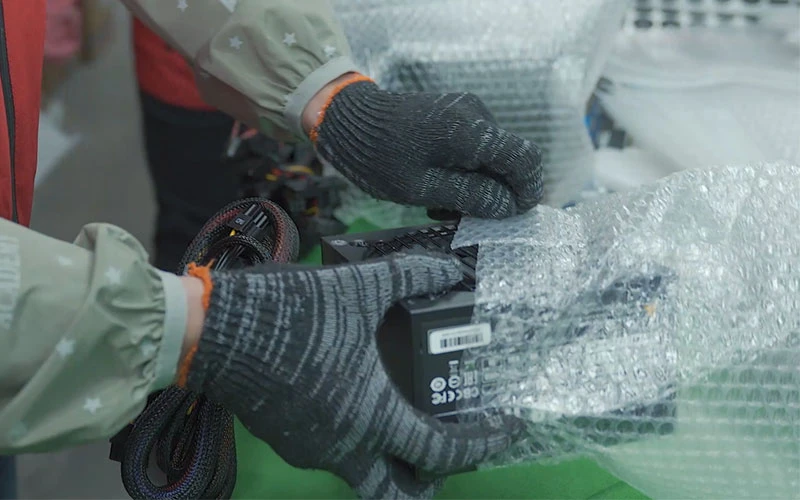
نکات کلیدی کنترل کیفیت
موارد فوق 9 مرحله برای تولید یک منبع تغذیه رومیزی است. علاوه بر این، نکات زیر نیز باید مورد توجه قرار گیرد:
عمر خازن: خازن های ژاپنی یا تایوانی با کیفیت بالا (مانند Rubycon، Nippon Chemi-Con) را انتخاب کنید.
طراحی اتلاف گرما: سرعت فن و نویز را متعادل کنید تا از کنترل طولانی مدت دما اطمینان حاصل کنید.
کیفیت جوش: از تماس ضعیف ناشی از لحیم کاری کاذب و لحیم کاری سرد اجتناب کنید.
روندهای صنعت
کوچک سازی و چگالی توان بالا: مانند منبع تغذیه SFX با میزبان کوچک سازگار است.
کنترل دیجیتال: از پردازنده سیگنال دیجیتال (DSP) برای دستیابی به تنظیم هوشمند ولتاژ استفاده کنید.
طراحی کاملا ماژولار: کاربران می توانند کابل ها را برای کاهش شلوغی در شاسی سفارشی کنند.
از طریق فرآیند فوق، منابع تغذیه دسکتاپ باید تحت کنترل فرآیند و آزمایش دقیق از طراحی تا محصول نهایی قرار گیرند تا از قابلیت اطمینان، کارایی و ایمنی آن اطمینان حاصل شود. مارک های مختلف ممکن است در مواد (مانند خازن های تمام ژاپنی)، درجه اتوماسیون (مانند خطوط تولید SMT تمام رباتی) و استانداردهای آزمایش متفاوت باشند.