-
Bâtiment E, n° 65 Xingshan North Road, Liangtian, parc industriel Baisha, district de Baiyun, Guangzhou
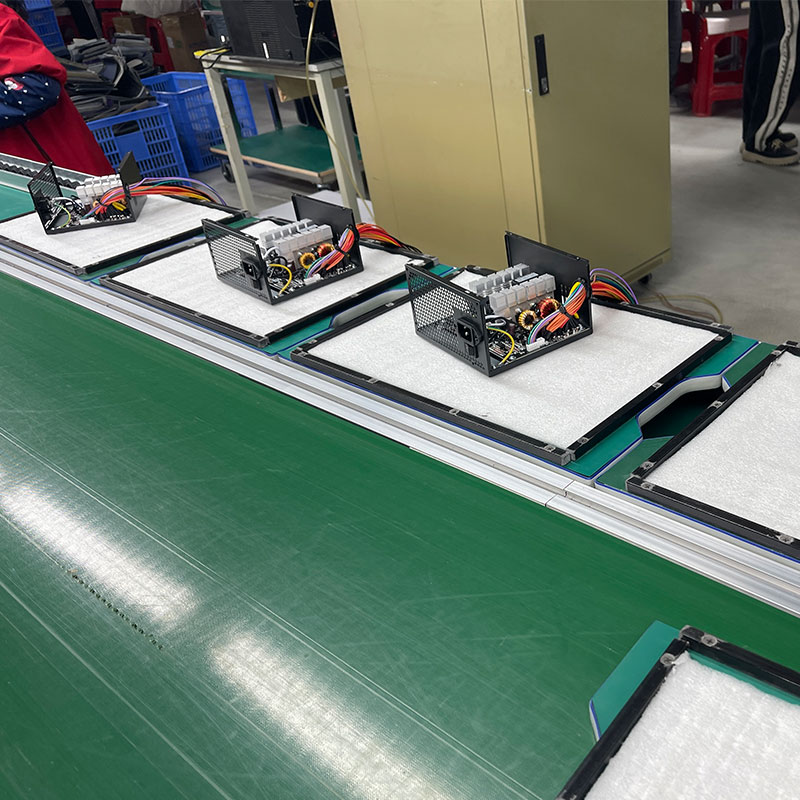
9 étapes pour fabriquer une alimentation de table
Le processus de production d'une alimentation de bureau (PC Power Supply Unit, PSU) implique plusieurs étapes, couvrant l'assemblage des composants électroniques, la conception des circuits, les tests de sécurité, etc. Voici 9 étapes pour produire une alimentation de table :
1. Conception et développement
Conception du circuit :
La conception et le développement des alimentations de bureau constituent le point de départ du processus de production et déterminent directement les performances, l'efficacité et la fiabilité du produit. Tout d'abord, les ingénieurs doivent définir les paramètres d'entrée et de sortie de l'alimentation conformément aux normes de l'industrie (telles que les spécifications Intel ATX), y compris la puissance nominale (telle que 500 W, 750 W), la plage de tension (+12 V, +5 V, +3,3 V, etc.) et le type d'interface (alimentation de carte mère 24 broches, PCIe 8 broches, etc.). La conception du circuit principal adopte généralement l'architecture « PFC actif + résonance LLC + redressement synchrone » pour obtenir une efficacité de conversion élevée (telle que la médaille d'or 80 PLUS ou supérieure). À ce stade, la stabilité de la structure topologique doit être vérifiée à l'aide d'un logiciel de simulation (tel que SPICE) pour garantir que la tension peut rester stable dans des conditions extrêmes telles que la mutation de charge et la température élevée.
Sélection des composants : sélectionnez les composants clés (tels que les condensateurs, les inducteurs, les MOSFET, les transformateurs, les dissipateurs thermiques, etc.), en tenant compte de l'efficacité (comme la certification 80 PLUS), de la densité de puissance et du coût.
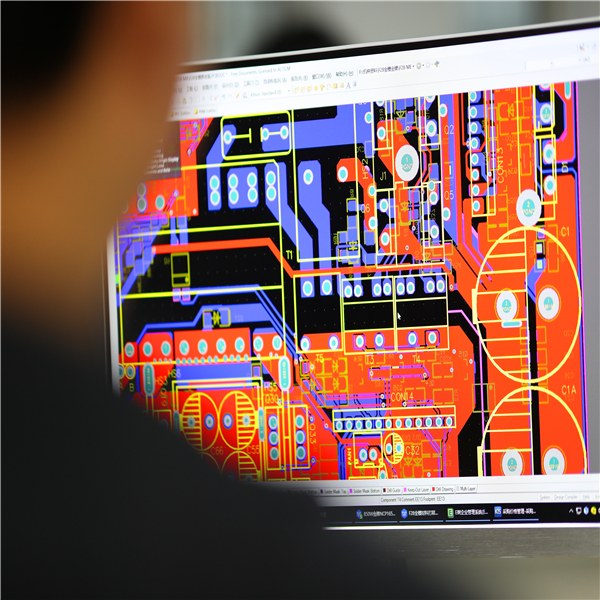
Vérification de la simulation :
En termes de sélection des composants, les composants clés doivent prendre en compte à la fois les performances et le coût : la puce de contrôle principale est principalement constituée de solutions taïwanaises (comme Great Wall) ou américaines (comme Texas Instruments) ; les condensateurs doivent être résistants aux températures élevées (supérieures à 105 °C) et avoir une longue durée de vie (comme le Nippon Chemi-Con japonais) ; et les ventilateurs de refroidissement doivent équilibrer le bruit (< 25 dB) et le volume d'air. De plus, l'équipe de conception doit optimiser la disposition du PCB, par exemple en isolant la zone haute tension (côté primaire) de la zone basse tension (côté secondaire), en réduisant les interférences électromagnétiques (EMI) et en réduisant l'impédance et la perte de chaleur grâce au câblage multicouche.
Disposition du PCB :
La phase de conception doit également prévoir les exigences de certification (telles que UL, CE, FCC) pour éviter à l'avance les interférences électromagnétiques dépassant la norme ou les risques de défaillance de l'isolation. Par exemple, les distances de sécurité (distances de fuite et distances d'isolement électrique) doivent être conformes à la norme IEC 60950, et le circuit PFC doit respecter les limites harmoniques IEC 61000-3-2. Enfin, les documents de conception (y compris les schémas de circuit, les listes de nomenclatures et les modèles structurels 3D) seront transférés à l'étape de production pour fournir des indications précises sur l'approvisionnement en matériaux et l'assemblage ultérieurs. Ce processus prend généralement plusieurs mois à six mois et constitue la base de la qualité de l'énergie.
2. Approvisionnement et contrôle des matières premières
L'approvisionnement et le contrôle des matières premières sont des éléments cruciaux dans la production d'alimentations pour PC, qui affectent directement la qualité et la fiabilité des produits. En termes d'approvisionnement en composants, nous contrôlons strictement la qualité des composants clés, tels que les condensateurs électrolytiques, les inducteurs PFC, les transformateurs principaux, les puces de contrôle IC et les ventilateurs, qui sont au cœur des performances de l'alimentation. Les matières premières que nous achetons doivent être conformes aux normes environnementales RoHS pour garantir la protection de l'environnement et la durabilité des produits.
L'inspection des matières premières entrantes (IQC) est la clé pour garantir que tous les composants entrant dans la chaîne de production répondent aux normes de qualité. Nous effectuons des inspections de qualité complètes sur les composants, notamment la capacité et la tension de tenue des condensateurs, la résistance à l'état passant des MOSFET et d'autres paramètres clés pour garantir qu'ils répondent pleinement aux exigences de conception. Notre processus IQC est rigoureux et méticuleux, et chaque lot de matières premières est rigoureusement testé pour empêcher tout composant non qualifié d'entrer dans le processus de production, garantissant ainsi l'excellente qualité et la fiabilité à long terme du produit final. Cela nous aide à garantir la qualité des produits et à fournir de meilleurs services.
3. Production de PCB
La production de PCB (Printed Circuit Board) est le maillon essentiel de la fabrication des alimentations PC. Elle assure une connexion et un support fiables pour les composants électroniques, tout comme le « squelette » de l'alimentation électrique. Notre processus de production de PCB respecte strictement les normes de l'industrie pour garantir que chaque PCB présente d'excellentes performances et une excellente durabilité.
Production de substrat :
Nous sélectionnons des substrats isolants de haute qualité, tels que des matériaux FR-4 ou de qualité supérieure, qui présentent d'excellentes propriétés d'isolation électrique et une résistance mécanique. Une feuille de cuivre est laminée sur le substrat isolant pour former un substrat PCB. L'épaisseur de la feuille de cuivre est généralement comprise entre 1 once (environ 35 microns) ou 2 onces (environ 70 microns), et le choix spécifique dépend du courant de conception et du niveau de tension de l'alimentation.
Photolithographie et gravure :
Nous utilisons la photolithographie pour transférer le motif du circuit sur le substrat PCB. Ce processus est similaire au processus de développement d'une photo, dans lequel le matériau photosensible est exposé conformément au schéma du circuit. Grâce à la gravure, nous éliminons l'excès de couche de cuivre, laissant les traces et les pastilles de circuit requises, formant ainsi le système de « vaisseaux sanguins » de l'alimentation électrique. La précision de la gravure peut généralement atteindre 0,1 mm ou moins pour répondre aux besoins de conception de circuits à haute densité.
Forage et dépôt de cuivre :
Il s'agit d'une étape clé dans la production de PCB. Nous utilisons des équipements de perçage de haute précision pour percer des trous traversants (vias) et des trous de broches de composants sur les PCB. Les trous traversants sont utilisés pour connecter différentes couches de PCB et fournir des canaux pour la transmission du courant. Le processus de placage au cuivre consiste à plaquer une couche de cuivre sur la paroi du trou percé pour assurer la conductivité du trou traversant. Le contrôle de la taille et de l'espacement des trous est crucial pour les performances électriques du PCB. Par exemple, le diamètre du trou traversant est généralement compris entre 0,3 mm et 0,6 mm pour répondre aux besoins de transmission du courant.
Masque de soudure et sérigraphie :
Nous appliquons de l'encre de masque de soudure, généralement verte ou d'autres couleurs, sur la surface du PCB pour protéger les traces du circuit de la corrosion et des courts-circuits. Le masque de soudure est également utilisé pour définir la zone de soudure du composant. Ensuite, nous imprimons l'identification du composant sur le PCB, comme le nombre de résistances et de condensateurs, pour faciliter l'assemblage et la maintenance ultérieurs des composants. L'épaisseur du masque de soudure est généralement comprise entre 15 microns et 30 microns pour assurer une bonne protection du circuit. Après ces processus rigoureux, chaque PCB atteindra des performances optimales.
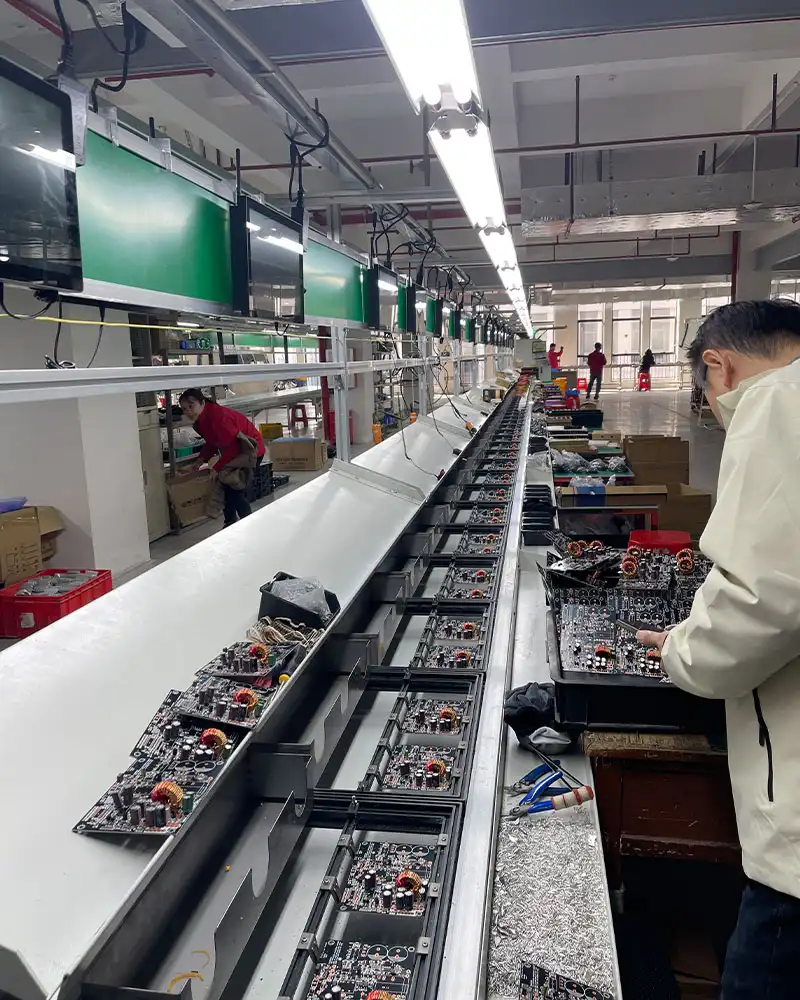
4. Installation des composants
Il s'agit d'une étape clé dans l'assemblage de l'alimentation d'un PC. Elle relie le « squelette » du PCB à divers composants électroniques pour former le « cœur » de l'alimentation. Notre processus d'installation des composants utilise la technologie avancée SMT (montage en surface) et la technologie enfichable traditionnelle pour garantir une installation précise et une connexion fiable des composants.
Patch SMT :
À l'aide de machines de soudage de haute précision, nous soudons avec précision de petits composants tels que des résistances, des condensateurs, des puces de circuits intégrés, etc. aux pastilles du PCB. La machine de soudage peut réaliser un soudage à grande vitesse et de haute précision, et la précision du soudage peut généralement atteindre 0,1 mm. Ensuite, nous utilisons le processus de soudage par refusion pour faire fondre la pâte à souder afin que les composants soient fermement fixés sur le PCB. La courbe de température du soudage par refusion est contrôlée avec précision pour garantir la qualité du soudage.
Installation des composants :
Il est destiné aux composants de grande taille, tels que les condensateurs électrolytiques, les transformateurs et les broches de dissipateur thermique. Ces composants sont généralement de grande taille et ne peuvent pas être réparés par CMS. Nos ouvriers insèrent ces composants dans les trous correspondants du PCB manuellement ou à la machine pendant le processus de branchement. Le branchement manuel garantit la flexibilité et la précision de l'installation, tandis que le branchement à la machine améliore l'efficacité et la cohérence.
Soudure à la vague :
Soudure de composants enfichables pour former des connexions électriques fiables. La soudure à la vague consiste à immerger le PCB dans de la soudure fondue afin que la soudure mouille les broches des composants et forme des joints de soudure. La température et la durée de la soudure à la vague sont contrôlées avec précision pour garantir la qualité de la soudure. Grâce à ces processus rigoureux, chaque alimentation est assemblée pour des performances optimales.
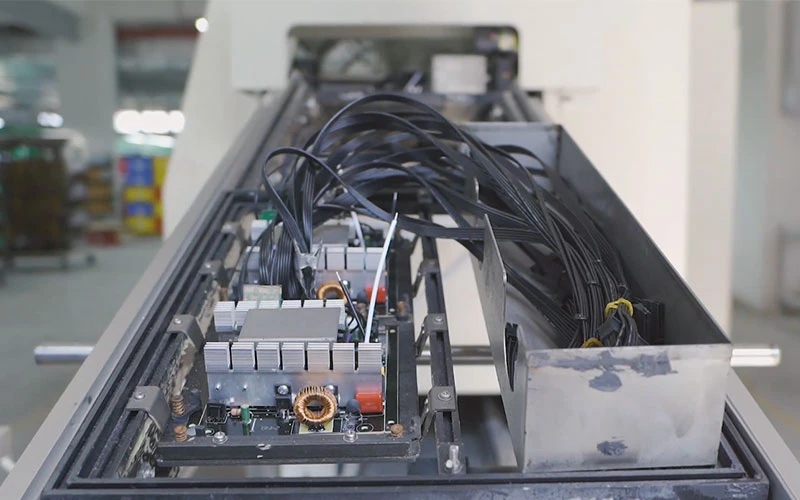
5. Assemblage du module clé
Il s'agit du maillon central de la fabrication des alimentations PC. Ces modules déterminent directement les performances, l'efficacité et la fiabilité de l'alimentation. Nous utilisons des processus précis et un contrôle qualité strict dans l'assemblage des modules clés pour garantir que chaque module puisse atteindre des performances optimales.
Module PFC (correction du facteur de puissance) :
Nous installerons des circuits de correction du facteur de puissance actifs ou passifs pour améliorer l'utilisation de l'énergie. Les circuits PFC actifs peuvent améliorer considérablement le facteur de puissance de l'alimentation électrique à près de 1, réduisant ainsi les pertes de puissance réactive dans le réseau électrique et répondant aux normes d'efficacité énergétique. Nous assurerons la qualité et l'installation de composants clés tels que les inducteurs PFC pour garantir les performances des modules PFC.
Module transformateur principal et redresseur :
Nous assemblerons des transformateurs haute fréquence pour isoler le courant alternatif et ajuster la tension. La qualité et la conception du transformateur sont cruciales pour l'efficacité et la stabilité de l'alimentation électrique. Dans le même temps, nous assemblerons également des circuits de redressement, tels que des diodes de redressement synchrones ou Schottky. Ces composants sont utilisés pour convertir le courant alternatif en courant continu afin de fournir la tension requise pour divers composants de l'ordinateur. La sélection et l'installation correctes de ces composants sont cruciales pour la qualité de sortie de l'alimentation électrique.
Circuit de refroidissement:
Étant donné que l'alimentation électrique génère de la chaleur pendant son fonctionnement, le système de refroidissement est crucial. Nous allons fixer le dissipateur thermique, généralement en alliage d'aluminium, pour augmenter la zone de dissipation thermique. Nous appliquerons également du silicone thermoconducteur pour améliorer la conduction thermique entre le dissipateur thermique et l'élément chauffant. De plus, nous installerons un ventilateur de refroidissement, généralement un ventilateur de 12 cm ou 14 cm, pour assurer une circulation d'air efficace, évacuer la chaleur de l'intérieur de l'alimentation électrique et assurer un fonctionnement stable de l'alimentation électrique.
6. Assemblage du module de puissance
Il s'agit du dernier processus de fabrication d'une alimentation PC, qui intègre tous les composants internes pour former une alimentation complète et utilisable. Dans ce lien, nous prêtons attention à chaque détail pour assurer la sécurité, la stabilité et la beauté de l'alimentation.
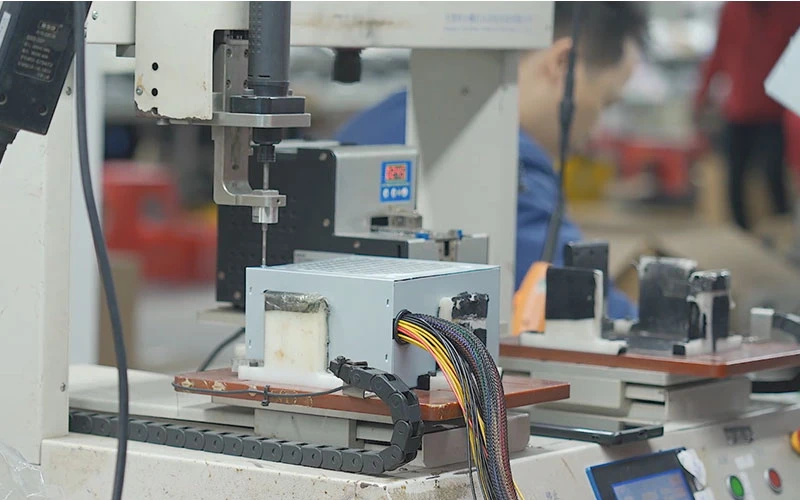
Ensemble boîtier :
Nous installons des composants internes tels que des circuits imprimés (PCB), des ventilateurs, des interrupteurs, etc. dans le boîtier métallique, qui est généralement constitué de plaques d'acier galvanisé pour assurer une protection solide et un bon effet de blindage EMI (interférence électromagnétique). Le blindage EMI peut empêcher efficacement le rayonnement électromagnétique à l'intérieur de l'alimentation d'interférer avec d'autres appareils électroniques et réduire l'impact des interférences électromagnétiques externes sur l'alimentation. Pendant le processus d'assemblage du boîtier, nous nous assurons que tous les composants sont fermement fixés dans le boîtier et étroitement connectés au boîtier.
Soudure de câbles :
Nous connecterons divers câbles de sortie, notamment l'alimentation de la carte mère 24 broches, l'alimentation PCIe, l'alimentation SATA, etc., qui sont utilisés pour alimenter divers composants de l'ordinateur. La qualité de la soudure est directement liée à la stabilité et à la fiabilité de l'alimentation. Nous utilisons des matériaux et des procédés de soudage de haute qualité pour garantir que les points de soudure sont solides et fiables. Après le soudage, nous placerons des manchons isolants sur les câbles pour éviter les courts-circuits et autres risques de sécurité.
Fixation et Isolation :
Nous utilisons des vis pour fixer les composants internes afin d'éviter qu'ils ne bougent ou ne se desserrent pendant le transport ou l'utilisation. Pour améliorer encore la sécurité de l'alimentation électrique, nous ajoutons également des feuilles isolantes ou des tampons en caoutchouc pour éviter les courts-circuits entre les composants internes. Le matériau et l'épaisseur de la feuille isolante sont soigneusement sélectionnés pour assurer une bonne isolation. Grâce à ces processus, chaque module d'alimentation obtiendra un effet sûr, stable et fiable.
7. Test et étalonnage
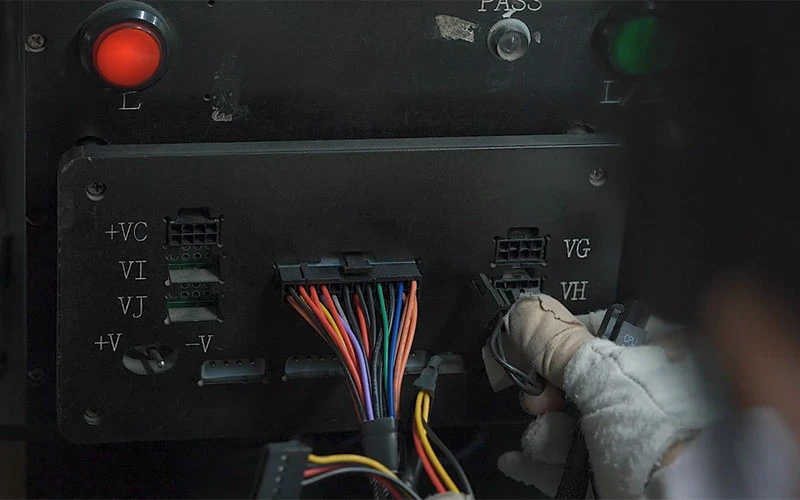
Test de mise sous tension :
Vérifiez si la tension à vide et l'alimentation de secours (+5VSB) sont normales.
Test de charge : simulez un fonctionnement à pleine charge pour vérifier la stabilité de chaque sortie de tension (+12 V, +5 V, +3,3 V).
Test de la fonction de protection :
protection contre les surtensions de déclenchement (OVP), protection contre les surintensités (OCP), protection contre les courts-circuits (SCP), etc.
Test d'efficacité et d'ondulation :
mesurer l'efficacité de conversion (comme les exigences de certification 80 PLUS) et l'ondulation de sortie (doit être conforme aux normes Intel ATX).
Test de rodage : exécuté en continu pendant plusieurs heures pour détecter les premiers composants défectueux.
8. Certification et contrôle de conformité
Certification de sécurité : passez les certifications UL, CE, FCC, CCC et autres pour garantir la conformité aux normes de sécurité régionales.
Certification d'efficacité énergétique : demandez la certification 80 PLUS (bronze/or/titane, etc.) et marquez le niveau d'efficacité.
Test EMI/EMC : garantit que le rayonnement électromagnétique est conforme à la réglementation pour éviter les interférences avec d'autres appareils.
9. Emballage et expédition
Contrôle d'apparence : nettoyer le boîtier et vérifier l'absence de rayures ou de défauts d'assemblage.
Emballage des accessoires : cordon d'alimentation, vis, manuel, etc. sont inclus.
Code-barres et traçabilité : l'étiquette du numéro de série SN est apposée pour une traçabilité qualité aisée.
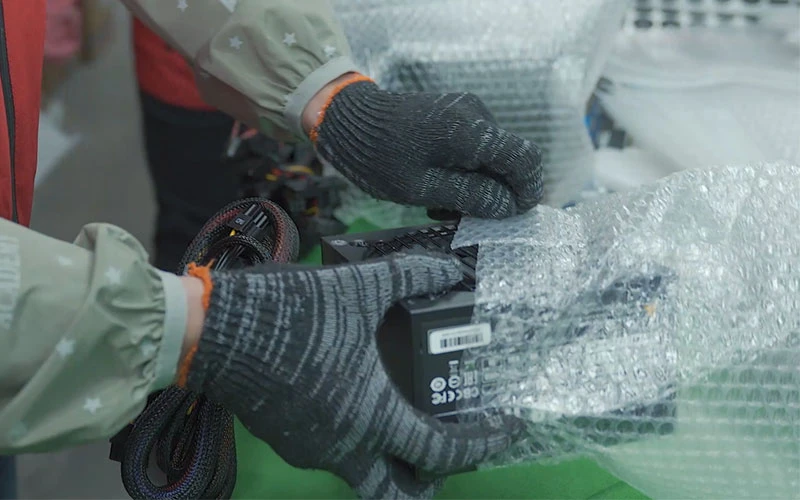
Points clés du contrôle qualité
Les 9 étapes ci-dessus permettent de fabriquer une alimentation électrique de table. De plus, les points suivants doivent être pris en compte :
Durée de vie du condensateur : sélectionnez des condensateurs japonais ou taïwanais de haute qualité (tels que Rubycon, Nippon Chemi-Con).
Conception de dissipation thermique : équilibrez la vitesse du ventilateur et le bruit pour assurer un contrôle de la température à long terme.
Qualité de soudure : Evitez les mauvais contacts causés par les fausses soudures et les soudures à froid.
Tendances de l'industrie
Miniaturisation et haute densité de puissance : l'alimentation SFX s'adapte aux petits hôtes.
Contrôle numérique : utilisez un processeur de signal numérique (DSP) pour obtenir une régulation de tension intelligente.
Conception entièrement modulaire : les utilisateurs peuvent personnaliser les câbles pour réduire l'encombrement dans le châssis.
Grâce au processus ci-dessus, les alimentations de bureau doivent subir un contrôle de processus et des tests stricts de la conception au produit fini pour garantir leur fiabilité, leur efficacité et leur sécurité. Différentes marques peuvent différer en termes de matériaux (tels que les condensateurs entièrement japonais), de degré d'automatisation (comme les lignes de production SMT entièrement robotisées) et de normes de test.