-
広州市白雲区白沙工業園梁天市興山北路65号建物E
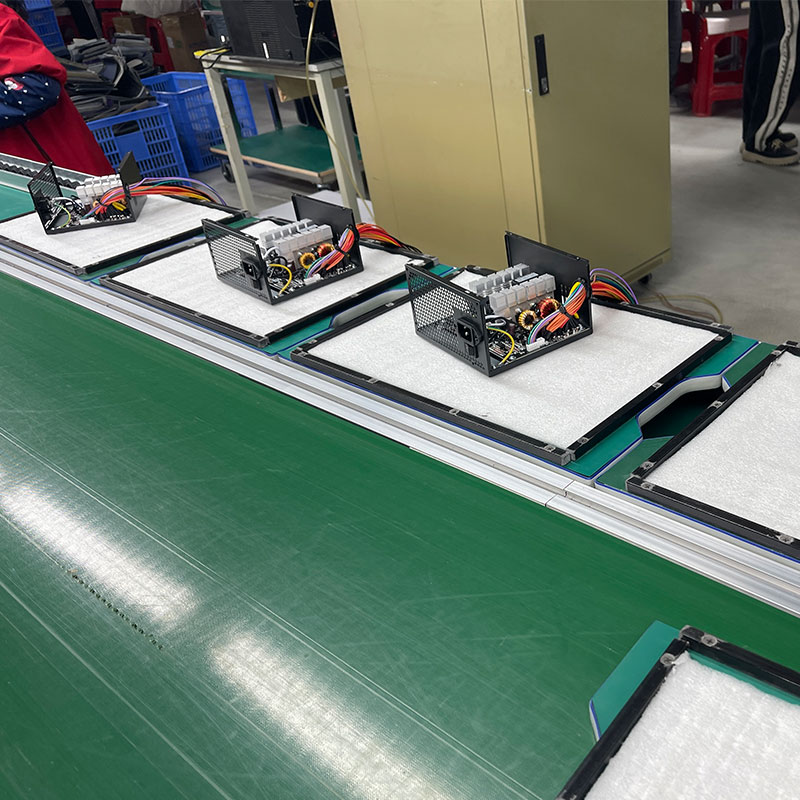
ベンチトップ電源を製造するための 9 つのステップ
デスクトップ電源(PC電源ユニット、PSU)の製造プロセスには、電子部品の組み立て、回路設計、安全性テストなど、複数のリンクが含まれます。以下は、ベンチトップ電源を製造するための9つのステップです。
1. 設計と開発
回路設計:
デスクトップ電源の設計と開発は、生産プロセスの出発点であり、製品の性能、効率、信頼性を直接決定します。まず、エンジニアは業界標準(Intel ATX仕様など)に従って、定格電力(500W、750Wなど)、電圧範囲(+12V、+5V、+3.3Vなど)、インターフェイスタイプ(24ピンマザーボード電源、PCIe 8ピンなど)を含む電源の入力および出力パラメータを定義する必要があります。コア回路設計では通常、「アクティブPFC + LLC共振+同期整流」アーキテクチャを採用し、高い変換効率(80 PLUSゴールドメダル以上など)を実現します。この段階では、シミュレーションソフトウェア(SPICEなど)を使用してトポロジ構造の安定性を検証し、負荷変動や高温などの極端な条件下でも電圧が安定していることを保証する必要があります。
コンポーネントの選択: 効率 (80 PLUS 認証など)、電力密度、コストを考慮して、主要コンポーネント (コンデンサ、インダクタ、MOSFET、トランス、ヒートシンクなど) を選択します。
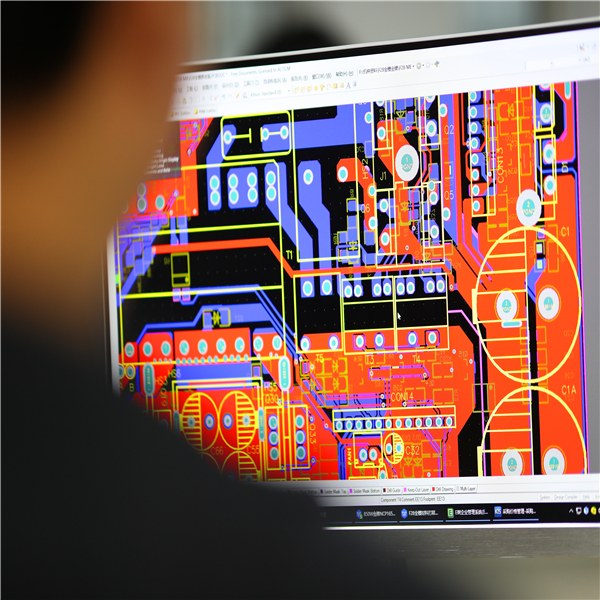
シミュレーション検証:
部品の選択に関しては、主要な部品は性能とコストの両方を考慮する必要があります。主な制御チップは主に台湾製(Great Wallなど)または米国製(Texas Instrumentsなど)のソリューションです。コンデンサは高温耐性(105°C以上)と長寿命(日本の日本ケミコンなど)を満たす必要があります。冷却ファンは騒音(<25dB)と風量のバランスをとる必要があります。さらに、設計チームは、高電圧領域(一次側)と低電圧領域(二次側)を分離し、電磁干渉(EMI)を減らし、多層配線によってインピーダンスと熱損失を減らすなど、PCBレイアウトを最適化する必要があります。
PCBレイアウト:
設計段階では、EMIが規格を超えたり、絶縁不良のリスクを事前に回避するために、認証要件(UL、CE、FCCなど)も予測する必要があります。たとえば、安全距離(沿面距離と電気的クリアランス)はIEC 60950規格に準拠する必要があり、PFC回路はIEC 61000-3-2高調波制限を満たす必要があります。最後に、設計ドキュメント(回路図、BOMリスト、3D構造モデルを含む)が製造段階に転送され、その後の材料調達と組み立てに正確なガイダンスを提供します。このプロセスは通常、数か月から半年かかり、電力品質の基礎となります。
2. 原材料調達と検査
原材料の調達と検査は、PC 電源の生産において非常に重要な部分であり、製品の品質と信頼性に直接影響します。部品調達の面では、電源性能の中核となる電解コンデンサ、PFC インダクタ、主変圧器、IC 制御チップ、ファンなどの主要部品の品質を厳しく管理しています。当社が購入する原材料は、製品の環境保護と持続可能性を確保するために、RoHS 環境基準に準拠している必要があります。
受入材料検査(IQC)は、生産ラインに入るすべての部品が品質基準を満たしていることを確認するための鍵です。コンデンサの容量と耐電圧、MOSFETのオン抵抗、その他の重要なパラメータを含む部品の包括的な品質検査を実施し、設計要件を完全に満たしていることを確認します。当社のIQCプロセスは厳格で細心の注意を払っており、原材料の各バッチは厳密にテストされ、不適格な部品が生産プロセスに入るのを防ぎ、最終製品の優れた品質と長期的な信頼性を保証します。これにより、製品の品質を保証し、より良いサービスを提供できます。
3. PCB製造
PCB (プリント回路基板) の製造は、PC 電源製造の中核です。電源の「骨格」のように、電子部品に信頼性の高い接続とサポートを提供します。当社の PCB 製造プロセスは、業界標準に厳密に従い、各 PCB が優れた性能と耐久性を備えていることを保証します。
基板製造:
当社では、優れた電気絶縁性と機械的強度を備えた FR-4 以上のグレードの材料などの高品質の絶縁基板を選択します。銅箔を絶縁基板に積層して PCB 基板を形成します。銅箔の厚さは通常 1 オンス (約 35 ミクロン) または 2 オンス (約 70 ミクロン) の間であり、具体的な選択は電源の設計電流と電圧レベルによって異なります。
フォトリソグラフィーとエッチング:
フォトリソグラフィーを使用して、回路パターンを PCB 基板に転写します。これは、回路図に従って感光材料を露光する写真の現像プロセスに似ています。エッチングにより余分な銅層を取り除き、必要な回路トレースとパッドを残して、電源の「血管」システムを形成します。エッチングの精度は通常 0.1 mm 以下に達し、高密度回路設計のニーズを満たします。
掘削と銅の堆積:
これは PCB 製造における重要なステップです。当社では高精度のドリル装置を使用して、PCB にスルーホール (ビア) とコンポーネント ピン ホールをドリルで開けます。スルーホールは、PCB の異なる層を接続し、電流を伝送するためのチャネルを提供するために使用されます。銅メッキ プロセスは、ドリルで開けた穴の壁に銅の層をメッキして、スルーホールの導電性を確保することです。穴のサイズと間隔の制御は、PCB の電気的性能にとって重要です。たとえば、スルーホールの直径は、電流伝送のニーズを満たすために、通常 0.3 mm から 0.6 mm の間です。
はんだマスクとシルクスクリーン:
通常は緑色またはその他の色のはんだマスク インクを PCB の表面に塗布して、回路トレースを腐食や短絡から保護します。はんだマスクは、コンポーネントのはんだ付け領域を定義するためにも使用されます。次に、抵抗器やコンデンサの数などのコンポーネント ID を PCB に印刷して、その後のコンポーネントの組み立てとメンテナンスを容易にします。はんだマスクの厚さは、回路の保護を確実にするために、通常 15 ミクロンから 30 ミクロンです。これらの厳格なプロセスを経て、各 PCB は最適なパフォーマンスを実現します。
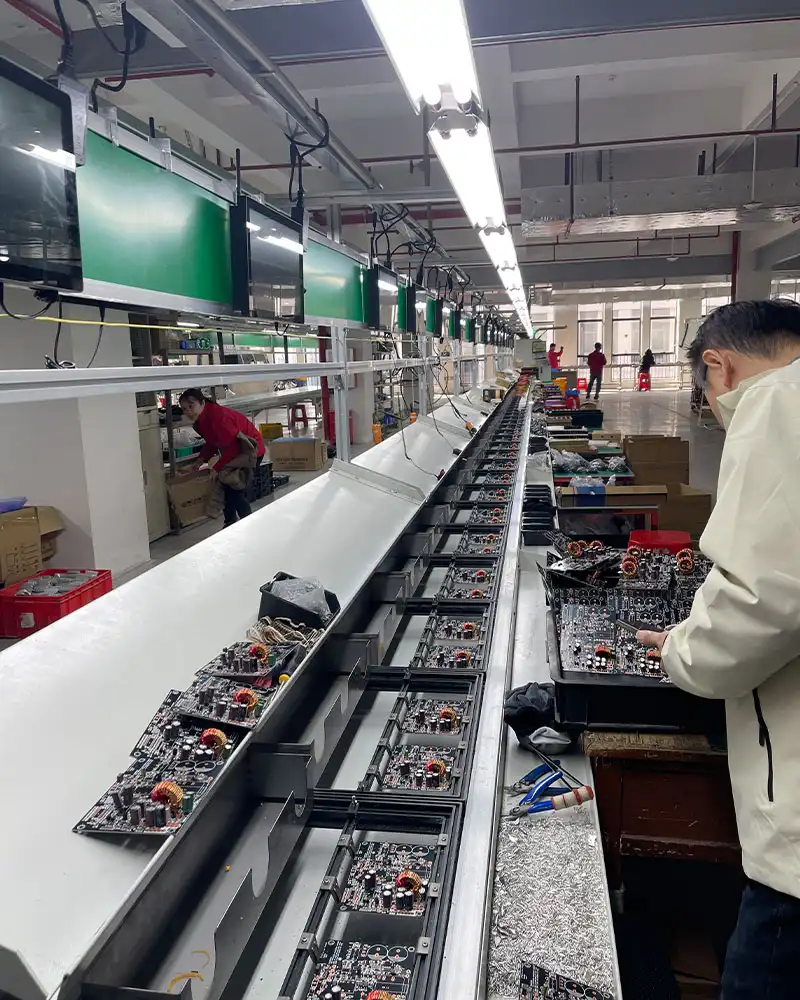
4. コンポーネントのインストール
これは PC 電源アセンブリの重要なステップです。PCB 上の「スケルトン」をさまざまな電子部品に接続して、電源の「心臓部」を形成します。当社の部品取り付けプロセスでは、高度な SMT (表面実装技術) と従来のプラグイン技術を使用して、部品の正確な取り付けと信頼性の高い接続を保証します。
SMTパッチ:
高精度のパッチマシンの助けを借りて、抵抗器、コンデンサ、ICチップなどの小さな部品をPCBのパッドに正確にはんだ付けします。パッチマシンは高速で高精度のパッチングを実現でき、パッチ精度は通常0.1mmに達します。次に、リフローはんだ付けプロセスを使用してはんだペーストを溶かし、部品をPCBにしっかりと固定します。リフローはんだ付けの温度曲線は、溶接の品質を確保するために正確に制御されています。
コンポーネントのインストール:
これは、電解コンデンサ、トランス、ヒートシンクピンなどの大型コンポーネント用です。これらのコンポーネントは通常サイズが大きく、SMT でパッチを当てることはできません。当社の作業員は、プラグイン プロセス中にこれらのコンポーネントを PCB の対応する穴に手動または機械で挿入します。手動プラグインは設置の柔軟性と精度を確保し、機械プラグインは効率と一貫性を向上させます。
ウェーブはんだ付け:
プラグイン コンポーネントをはんだ付けして、信頼性の高い電気接続を形成します。ウェーブはんだ付けでは、PCB を溶融はんだに浸し、はんだがコンポーネント ピンを濡らしてはんだ接合部を形成します。ウェーブはんだ付けの温度と時間は、はんだ付けの品質を確保するために正確に制御されます。これらの厳格なプロセスを通じて、各電源は最適なパフォーマンスで組み立てられます。
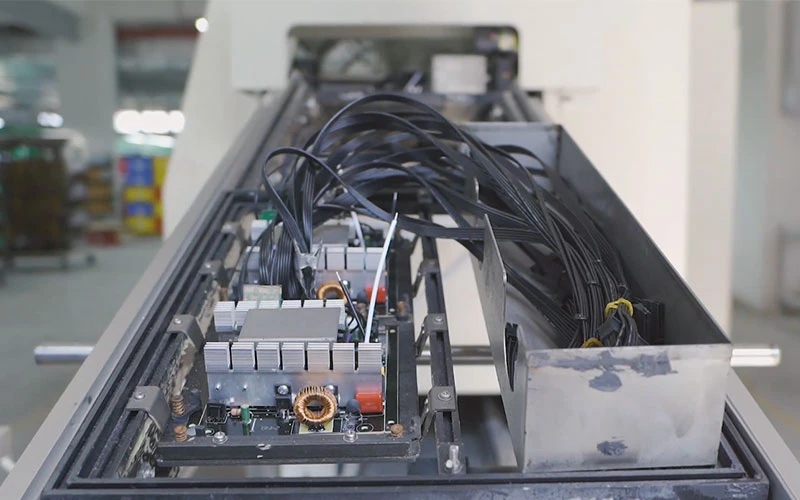
5. キーモジュールの組み立て
これは PC 電源製造の中核です。これらのモジュールは、電源のパフォーマンス、効率、信頼性を直接決定します。主要モジュールの組み立てには正確なプロセスと厳格な品質管理を採用し、各モジュールが最適なパフォーマンスを発揮できるようにします。
PFC(力率改善)モジュール:
アクティブまたはパッシブの力率補正回路を設置して、電力利用率を向上させます。アクティブ PFC 回路は、電源の力率を 1 に近づけるほど大幅に改善できるため、電力網の無効電力損失が削減され、エネルギー効率基準を満たすことができます。PFC インダクタなどの主要コンポーネントの品質と設置を確保して、PFC モジュールのパフォーマンスを確保します。
メイントランスおよび整流器モジュール:
高周波トランスを組み立てて、AC 電源を分離し、電圧を調整します。トランスの品質と設計は、電源の効率と安定性にとって重要です。同時に、同期整流やショットキー ダイオードなどの整流回路も組み立てます。これらのコンポーネントは、AC 電源を DC 電源に変換して、コンピューターのさまざまなコンポーネントに必要な電圧を提供するために使用されます。これらのコンポーネントを正しく選択して取り付けることは、電源の出力品質にとって非常に重要です。
冷却システム:
電源装置は動作中に熱を発生するため、冷却システムは非常に重要です。放熱面積を増やすために、通常はアルミニウム合金製のヒートシンクを固定します。また、ヒートシンクと発熱体の間の熱伝導を高めるために、熱伝導性シリコンを塗布します。さらに、効果的な空気循環を提供し、電源装置の内部から熱を取り除き、電源装置を安定して動作させるために、通常は12cmまたは14cmの冷却ファンを取り付けます。
6. パワーモジュールアセンブリ
これは PC 電源製造の最後のプロセスであり、すべての内部コンポーネントを統合して、完全で使用可能な電源を形成します。このリンクでは、電源の安全性、安定性、美しさを確保するために、細部にまで注意を払っています。
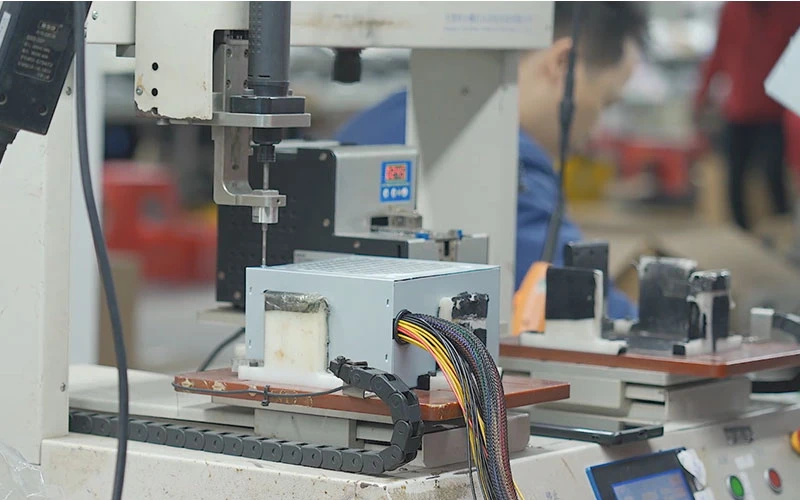
ケーシングアセンブリ:
当社では、PCB(プリント基板)、ファン、スイッチなどの内部部品を金属ケースに取り付けます。金属ケースは通常、亜鉛メッキ鋼板で作られており、堅牢な保護と優れたEMI(電磁干渉)シールド効果を提供します。EMIシールドは、電源装置内の電磁放射が他の電子機器に干渉するのを効果的に防ぎ、外部の電磁干渉が電源装置に与える影響を軽減します。ケースの組み立てプロセスでは、すべての部品がケース内にしっかりと固定され、ケースにしっかりと接続されていることを確認します。
ケーブル溶接:
24ピンマザーボード電源、PCIe電源、SATA電源など、コンピューターのさまざまなコンポーネントに電力を供給するために使用されるさまざまな出力ケーブルを接続します。溶接の品質は、電源の安定性と信頼性に直接関係しています。高品質の溶接材料とプロセスを使用して、溶接ポイントがしっかりと信頼性があることを保証します。溶接後、ケーブルに絶縁スリーブを付けて、短絡やその他の安全上の危険を防止します。
固定と断熱:
内部部品をネジで固定し、輸送中や使用中に部品が動いたり緩んだりしないようにします。電源の安全性をさらに向上させるために、内部部品間のショートを防ぐために絶縁シートやゴムパッドも追加しています。絶縁シートの材質と厚さは、良好な絶縁性を確保するために慎重に選択されています。これらのプロセスを通じて、各電源モジュールは安全で安定した信頼性の高い効果を実現します。
7. テストと校正
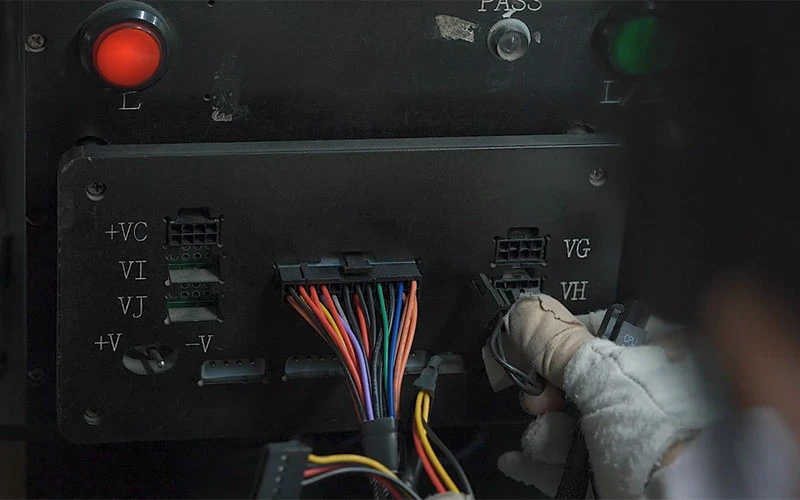
電源投入テスト:
無負荷電圧とスタンバイ電源(+5VSB)が正常かどうかを確認します。
負荷テスト: フル負荷動作をシミュレートして、各電圧出力 (+12V、+5V、+3.3V) の安定性を確認します。
保護機能テスト:
過電圧保護 (OVP)、過電流保護 (OCP)、短絡保護 (SCP) などをトリガーします。
効率とリップルテスト:
変換効率(80 PLUS 認証要件など)と出力リップル(Intel ATX 標準に準拠している必要があります)を測定します。
バーンイン テスト: 数時間連続して実行し、早期に故障したコンポーネントをスクリーニングします。
8. 認証およびコンプライアンス検査
安全認証: UL、CE、FCC、CCC などの認証に合格し、地域の安全基準に準拠していることを保証します。
エネルギー効率認証: 80 PLUS (ブロンズ/ゴールド/チタンなど) 認証を申請し、効率レベルをマークします。
EMI/EMC テスト: 他のデバイスとの干渉を避けるために、電磁放射が規制に準拠していることを確認します。
9. 梱包と発送
外観検査:筐体を清掃し、傷や組み立て不良がないか確認します。
付属品パッケージ:電源コード、ネジ、マニュアルなどが付属します。
バーコードとトレーサビリティ: SN シリアル番号ラベルが付属しており、品質のトレーサビリティが容易です。
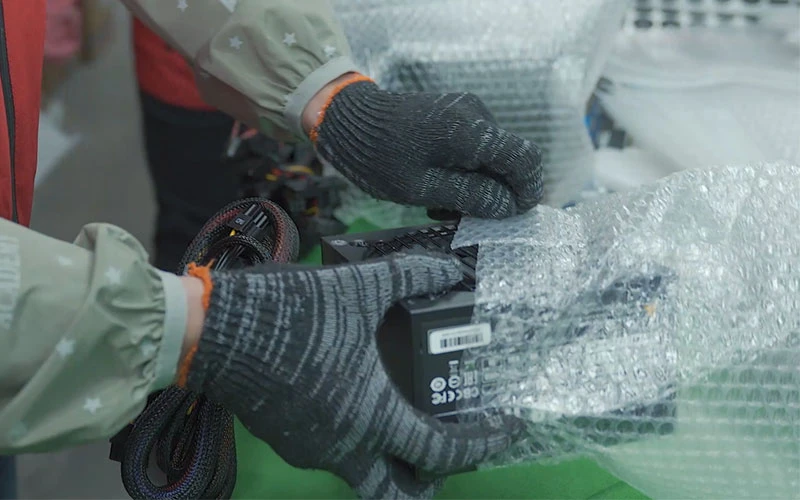
重要な品質管理ポイント
上記はベンチトップ電源を製造するための 9 つのステップです。さらに、以下の点に注意する必要があります。
コンデンサの寿命: 高品質の日本製または台湾製のコンデンサ (Rubycon、日本ケミコンなど) を選択します。
放熱設計: ファンの速度とノイズのバランスをとり、長期的な温度制御を実現します。
溶接品質: 誤ったはんだ付けや冷間はんだ付けによる接触不良を回避します。
業界動向
小型化と高電力密度: SFX 電源などは小型ホストに適応します。
デジタル制御: デジタル信号プロセッサ (DSP) を使用して、インテリジェントな電圧調整を実現します。
完全モジュール設計: ユーザーはケーブルをカスタマイズして、シャーシ内の乱雑さを軽減できます。
上記のプロセスを通じて、デスクトップ電源は、信頼性、効率、安全性を確保するために、設計から完成品まで厳格なプロセス管理とテストを受ける必要があります。ブランドによって、材料(日本製コンデンサなど)、自動化の程度(全ロボット SMT 生産ラインなど)、テスト基準が異なる場合があります。