-
Edifício E, No. 65 Xingshan North Road, Liangtian, Parque Industrial Baisha, Distrito de Baiyun, Guangzhou
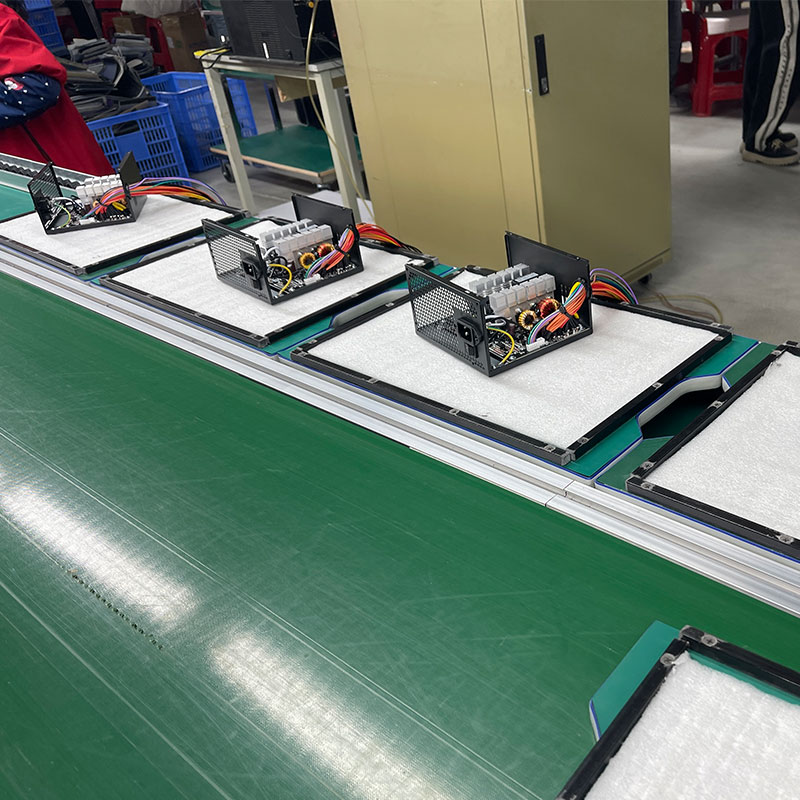
9 etapas para produzir uma fonte de alimentação de bancada
O processo de produção de uma fonte de alimentação de mesa (PC Power Supply Unit, PSU) envolve vários links, abrangendo montagem de componentes eletrônicos, projeto de circuito, testes de segurança, etc. A seguir estão 9 etapas para produzir uma fonte de alimentação de bancada:
1. Design e desenvolvimento
Projeto do circuito:
O design e o desenvolvimento de fontes de alimentação de mesa são o ponto de partida do processo de produção e determinam diretamente o desempenho, a eficiência e a confiabilidade do produto. Primeiro, os engenheiros precisam definir os parâmetros de entrada e saída da fonte de alimentação de acordo com os padrões da indústria (como as especificações Intel ATX), incluindo potência nominal (como 500 W, 750 W), faixa de tensão (+12 V, +5 V, +3,3 V, etc.) e tipo de interface (fonte de alimentação da placa-mãe de 24 pinos, PCIe de 8 pinos, etc.). O design do circuito principal geralmente adota a arquitetura de “ressonância PFC+LLC ativa+retificação síncrona” para atingir alta eficiência de conversão (como medalha de ouro 80 PLUS ou superior). Nesta fase, a estabilidade da estrutura da topologia precisa ser verificada por meio de software de simulação (como SPICE) para garantir que a tensão possa permanecer estável sob condições extremas, como mutação de carga e alta temperatura.
Seleção de componentes: selecione os principais componentes (como capacitores, indutores, MOSFETs, transformadores, dissipadores de calor, etc.), considerando a eficiência (como a certificação 80 PLUS), a densidade de potência e o custo.
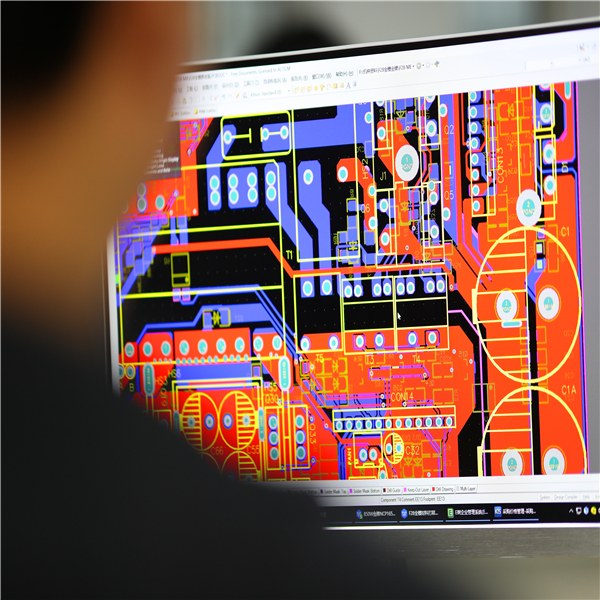
Verificação de simulação:
Em termos de seleção de componentes, os principais componentes precisam levar em conta tanto o desempenho quanto o custo: o chip de controle principal é principalmente soluções taiwanesas (como Great Wall) ou americanas (como Texas Instruments); os capacitores precisam atender à alta resistência à temperatura (acima de 105 °C) e longa vida útil (como o japonês Nippon Chemi-Con); e os ventiladores de resfriamento precisam equilibrar o ruído (<25 dB) e o volume de ar. Além disso, a equipe de design precisa otimizar o layout do PCB, como isolar a área de alta tensão (lado primário) da área de baixa tensão (lado secundário), reduzir a interferência eletromagnética (EMI) e reduzir a impedância e a perda de calor por meio da fiação multicamadas.
Layout da placa de circuito impresso:
O estágio de projeto também precisa prever requisitos de certificação (como UL, CE, FCC) para evitar que EMI exceda o padrão ou riscos de falha de isolamento com antecedência. Por exemplo, distâncias de segurança (distâncias de fuga e folgas elétricas) devem estar em conformidade com o padrão IEC 60950, e o circuito PFC deve atender aos limites harmônicos IEC 61000-3-2. Finalmente, os documentos de projeto (incluindo diagramas de circuito, listas de BOM e modelos estruturais 3D) serão transferidos para o estágio de produção para fornecer orientação precisa para aquisição e montagem de material subsequentes. Esse processo geralmente leva de vários meses a meio ano e é a base da qualidade de energia.
2. Aquisição e inspeção de matéria-prima
A aquisição e inspeção de matéria-prima são elos cruciais na produção de fontes de alimentação de PC, que afetam diretamente a qualidade e a confiabilidade do produto. Em termos de aquisição de componentes, controlamos rigorosamente a qualidade dos principais componentes, como capacitores eletrolíticos, indutores PFC, transformadores principais, chips de controle IC e ventiladores, que são o núcleo do desempenho da fonte de alimentação. As matérias-primas que compramos devem estar em conformidade com os padrões ambientais RoHS para garantir a proteção ambiental e a sustentabilidade dos produtos.
A inspeção de material de entrada (IQC) é a chave para garantir que todos os componentes que entram na linha de produção atendam aos padrões de qualidade. Realizamos inspeções de qualidade abrangentes em componentes, incluindo a capacidade e a tensão de resistência dos capacitores, a resistência de MOSFETs e outros parâmetros importantes para garantir que eles atendam totalmente aos requisitos de design. Nosso processo IQC é rigoroso e meticuloso, e cada lote de matérias-primas é rigorosamente testado para evitar que quaisquer componentes não qualificados entrem no processo de produção, garantindo assim a excelente qualidade e a confiabilidade de longo prazo do produto final. Isso nos ajuda a garantir a qualidade do produto e a fornecer melhores serviços.
3. Produção de PCB
A produção de PCB (Printed Circuit Board) é o elo principal da fabricação de fontes de alimentação para PC. Ela fornece conexão e suporte confiáveis para componentes eletrônicos, assim como o "esqueleto" da fonte de alimentação. Nosso processo de produção de PCB segue rigorosamente os padrões da indústria para garantir que cada PCB tenha excelente desempenho e durabilidade.
Produção de substrato:
Selecionamos substratos isolantes de alta qualidade, como FR-4 ou materiais de grau superior, que têm excelentes propriedades de isolamento elétrico e resistência mecânica. A folha de cobre é laminada ao substrato isolante para formar um substrato de PCB. A espessura da folha de cobre é geralmente entre 1 onça (cerca de 35 mícrons) ou 2 onças (cerca de 70 mícrons), e a escolha específica depende da corrente de projeto e do nível de tensão da fonte de alimentação.
Fotolitografia e gravura:
Usamos fotolitografia para transferir o padrão do circuito para o substrato do PCB. Isso é semelhante ao processo de desenvolvimento de uma foto, no qual o material fotossensível é exposto de acordo com o diagrama do circuito. Por meio da gravação, removemos o excesso de camada de cobre, deixando os traços e almofadas do circuito necessários, formando assim o sistema de "vasos sanguíneos" da fonte de alimentação. A precisão da gravação pode geralmente atingir 0,1 mm ou menos para atender às necessidades do design de circuito de alta densidade.
Perfuração e deposição de cobre:
É uma etapa fundamental na produção de PCB. Usamos equipamentos de perfuração de alta precisão para perfurar furos passantes (vias) e furos de pinos de componentes em PCBs. Os furos passantes são usados para conectar diferentes camadas de PCBs e fornecer canais para a transmissão de corrente. O processo de revestimento de cobre consiste em revestir uma camada de cobre na parede do furo perfurado para garantir a condutividade do furo passante. O controle do tamanho e espaçamento do furo é crucial para o desempenho elétrico do PCB. Por exemplo, o diâmetro do furo passante geralmente fica entre 0,3 mm e 0,6 mm para atender às necessidades de transmissão de corrente.
Máscara de solda e serigrafia:
Aplicamos tinta de máscara de solda, geralmente verde ou outras cores, na superfície do PCB para proteger os traços do circuito contra corrosão e curtos-circuitos. A máscara de solda também é usada para definir a área de soldagem do componente. Em seguida, imprimimos a identificação do componente no PCB, como o número de resistores e capacitores, para facilitar a montagem e manutenção subsequentes do componente. A espessura da máscara de solda é geralmente entre 15 mícrons e 30 mícrons para garantir uma boa proteção do circuito. Após esses processos rigorosos, cada PCB atingirá o desempenho ideal.
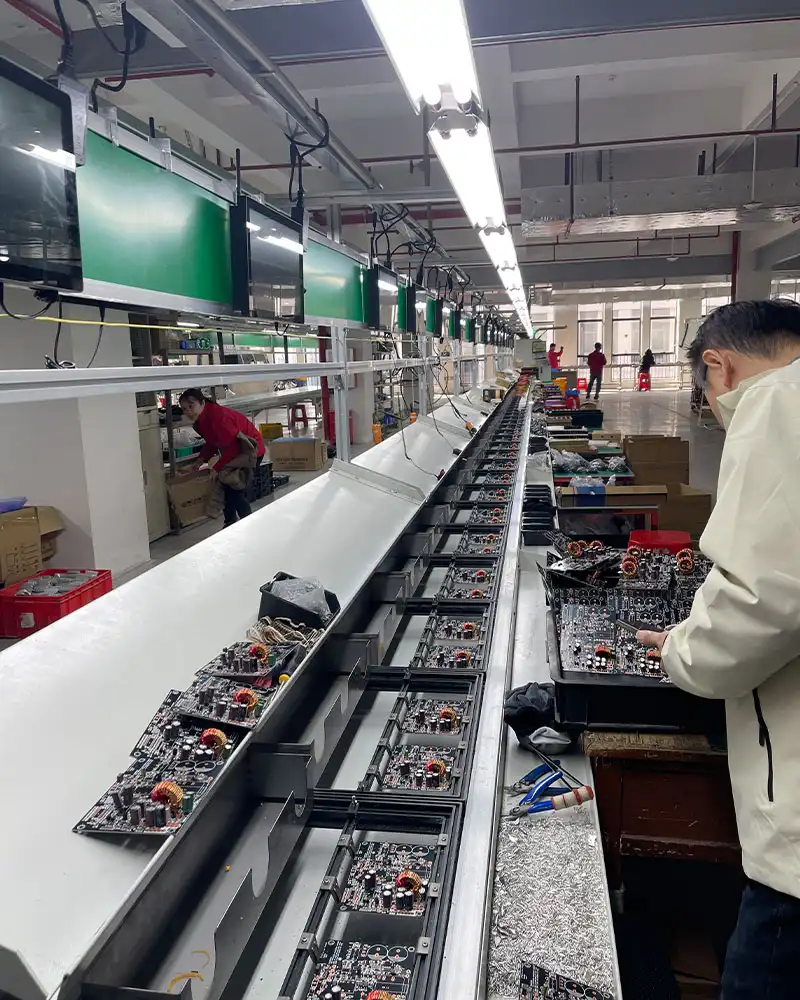
4. Instalação de componentes
É uma etapa fundamental na montagem da fonte de alimentação do PC. Ela conecta o “esqueleto” no PCB com vários componentes eletrônicos para formar o “coração” da fonte de alimentação. Nosso processo de instalação de componentes usa SMT (tecnologia de montagem em superfície) avançada e tecnologia plug-in tradicional para garantir a instalação precisa e a conexão confiável dos componentes.
Patch SMT:
Com a ajuda de máquinas de patch de alta precisão, soldamos com precisão pequenos componentes, como resistores, capacitores, chips IC, etc., às almofadas do PCB. A máquina de patch pode atingir patch de alta velocidade e alta precisão, e a precisão do patch geralmente pode atingir 0,1 mm. Em seguida, usamos o processo de soldagem por refluxo para derreter a pasta de solda para que os componentes fiquem firmemente fixados no PCB. A curva de temperatura da soldagem por refluxo é controlada com precisão para garantir a qualidade da soldagem.
Instalação de componentes:
É para componentes de grande porte, como capacitores eletrolíticos, transformadores e pinos de dissipador de calor. Esses componentes geralmente são grandes em tamanho e não podem ser remendados por SMT. Nossos trabalhadores inserem esses componentes nos furos correspondentes do PCB manualmente ou por máquina durante o processo de plug-in. O plug-in manual garante flexibilidade e precisão de instalação, enquanto o plug-in de máquina melhora a eficiência e a consistência.
Soldagem por onda:
soldar componentes plug-in para formar conexões elétricas confiáveis. Soldagem por onda é imergir o PCB em solda derretida para que a solda molhe os pinos do componente e forme juntas de solda. A temperatura e o tempo da soldagem por onda são controlados com precisão para garantir a qualidade da soldagem. Por meio desses processos rigorosos, cada fonte de alimentação é montada para desempenho ideal.
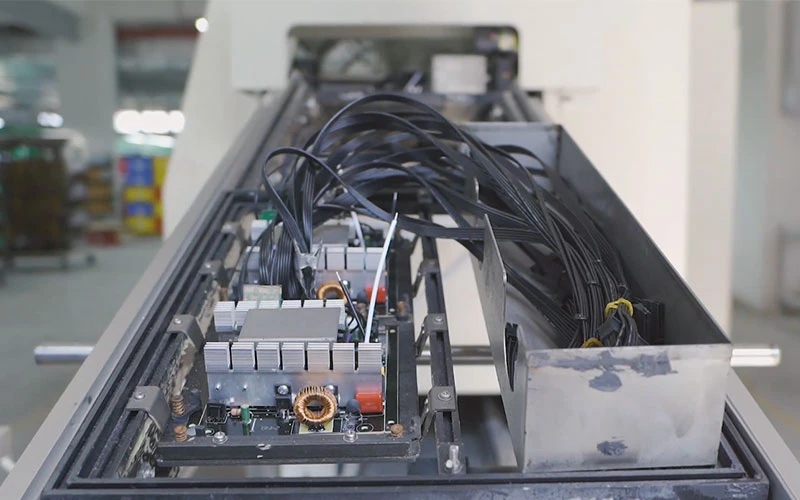
5. Montagem do módulo de chave
É o elo principal da fabricação de fontes de alimentação para PC. Esses módulos determinam diretamente o desempenho, a eficiência e a confiabilidade da fonte de alimentação. Usamos processos precisos e controle de qualidade rigoroso na montagem dos principais módulos para garantir que cada módulo possa atingir o desempenho ideal.
Módulo PFC (Correção do Fator de Potência):
Instalaremos circuitos de correção de fator de potência ativos ou passivos para melhorar a utilização de energia. Os circuitos PFC ativos podem melhorar significativamente o fator de potência da fonte de alimentação para perto de 1, reduzindo assim as perdas de potência reativa na rede elétrica e atendendo aos padrões de eficiência energética. Garantiremos a qualidade e a instalação de componentes-chave, como indutores PFC, para garantir o desempenho dos módulos PFC.
Módulo principal transformador e retificador:
Montaremos transformadores de alta frequência para isolar a energia CA e ajustar a voltagem. A qualidade e o design do transformador são cruciais para a eficiência e estabilidade da fonte de alimentação. Ao mesmo tempo, também montaremos circuitos de retificação, como retificação síncrona ou diodos Schottky. Esses componentes são usados para converter energia CA em energia CC para fornecer a voltagem necessária para vários componentes do computador. A seleção e instalação corretas desses componentes são cruciais para a qualidade de saída da fonte de alimentação.
Sistema de refrigeração:
Como a fonte de alimentação gera calor durante a operação, o sistema de resfriamento é crucial. Vamos consertar o dissipador de calor, geralmente feito de liga de alumínio, para aumentar a área de dissipação de calor. Também aplicaremos silicone condutor térmico para melhorar a condução de calor entre o dissipador de calor e o elemento de aquecimento. Além disso, instalaremos um ventilador de resfriamento, geralmente de 12 cm ou 14 cm, para fornecer circulação de ar eficaz, remover o calor de dentro da fonte de alimentação e manter a fonte de alimentação funcionando de forma estável.
6. Conjunto do módulo de potência
É o último processo de fabricação de fonte de alimentação para PC, que integra todos os componentes internos para formar uma fonte de alimentação completa e utilizável. Neste link, prestamos atenção a cada detalhe para garantir a segurança, estabilidade e beleza da fonte de alimentação.
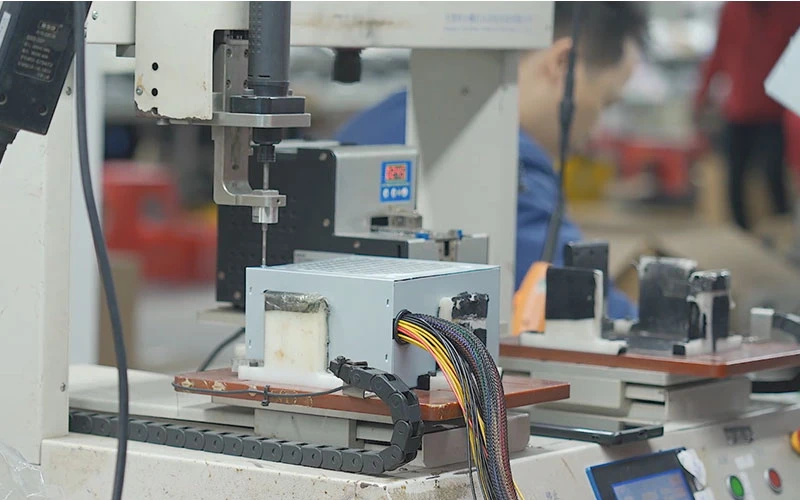
Conjunto de revestimento:
Instalamos componentes internos como PCB (placa de circuito impresso), ventilador, interruptor, etc. no invólucro de metal, que geralmente é feito de chapa de aço galvanizado para fornecer proteção sólida e bom efeito de blindagem EMI (interferência eletromagnética). A blindagem EMI pode efetivamente impedir que a radiação eletromagnética dentro da fonte de alimentação interfira com outros dispositivos eletrônicos e reduza o impacto da interferência eletromagnética externa na fonte de alimentação. Durante o processo de montagem do invólucro, garantimos que todos os componentes estejam firmemente fixados no invólucro e firmemente conectados ao invólucro.
Soldagem de cabos:
Conectaremos vários cabos de saída, incluindo fonte de alimentação de placa-mãe de 24 pinos, fonte de alimentação PCIe, fonte de alimentação SATA, etc., que são usados para fornecer energia a vários componentes do computador. A qualidade da soldagem está diretamente relacionada à estabilidade e confiabilidade da fonte de alimentação. Usamos materiais e processos de soldagem de alta qualidade para garantir que os pontos de soldagem sejam firmes e confiáveis. Após a soldagem, colocaremos mangas isolantes nos cabos para evitar curtos-circuitos e outros riscos à segurança.
Fixação e isolamento:
Usamos parafusos para fixar os componentes internos para evitar que eles se movam ou se soltem durante o transporte ou uso. Para melhorar ainda mais a segurança da fonte de alimentação, também adicionamos folhas isolantes ou almofadas de borracha para evitar curtos-circuitos entre os componentes internos. O material e a espessura da folha isolante são cuidadosamente selecionados para garantir um bom isolamento. Por meio desses processos, cada módulo de energia atingirá um efeito seguro, estável e confiável.
7. Teste e calibração
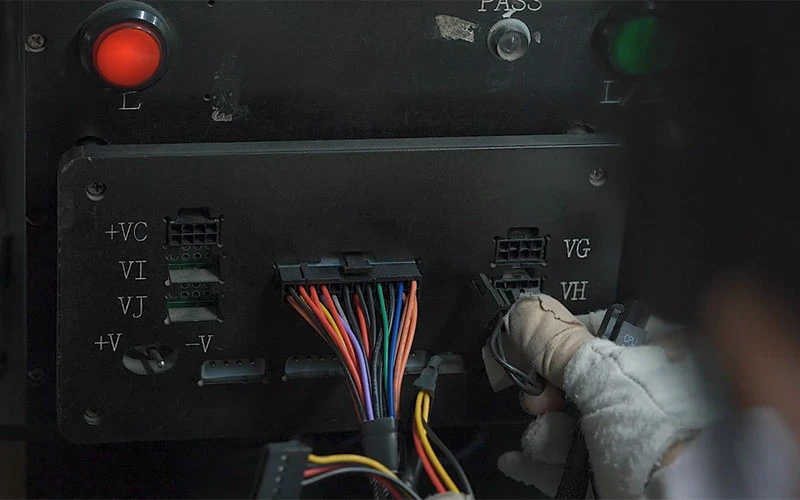
Teste de inicialização:
Verifique se a tensão sem carga e a fonte de alimentação de espera (+5VSB) estão normais.
Teste de carga: simule a operação em carga total para verificar a estabilidade de cada saída de tensão (+12 V, +5 V, +3,3 V).
Teste de função de proteção:
proteção contra sobretensão de gatilho (OVP), proteção contra sobrecorrente (OCP), proteção contra curto-circuito (SCP), etc.
Teste de eficiência e ondulação:
medir eficiência de conversão (como requisitos de certificação 80 PLUS) e ondulação de saída (deve estar em conformidade com os padrões Intel ATX).
Teste de burn-in: execute continuamente por várias horas para rastrear componentes com falhas precoces.
8. Certificação e inspeção de conformidade
Certificação de segurança: passe pelas certificações UL, CE, FCC, CCC e outras para garantir a conformidade com os padrões regionais de segurança.
Certificação de eficiência energética: solicite a certificação 80 PLUS (bronze/ouro/titânio, etc.) e marque o nível de eficiência.
Teste EMI/EMC: garanta que a radiação eletromagnética esteja em conformidade com as regulamentações para evitar interferência com outros dispositivos.
9. Embalagem e envio
Inspeção de aparência: limpe a caixa e verifique se há arranhões ou defeitos de montagem.
Embalagem de acessórios: cabo de alimentação, parafusos, manual, etc. estão incluídos.
Código de barras e rastreabilidade: a etiqueta com número de série SN é anexada para fácil rastreabilidade de qualidade.
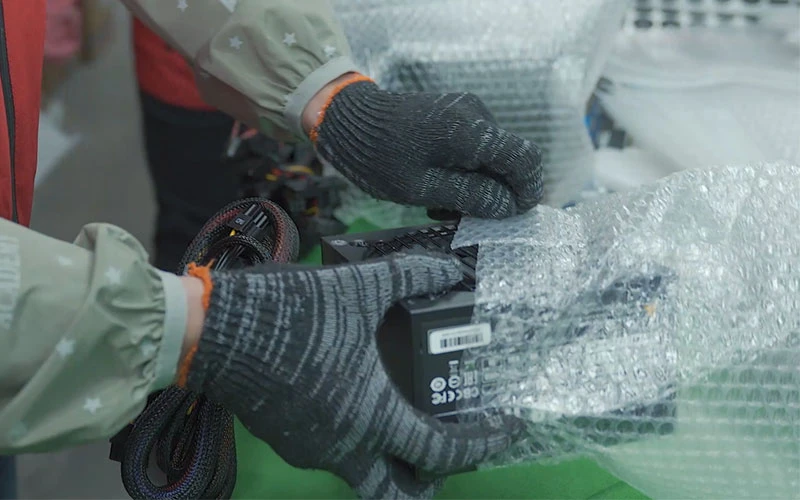
Principais pontos de controle de qualidade
Acima estão os 9 passos para produzir uma fonte de alimentação de bancada. Além disso, há os seguintes pontos que precisam de atenção:
Vida útil do capacitor: Selecione capacitores japoneses ou taiwaneses de alta qualidade (como Rubycon, Nippon Chemi-Con).
Design de dissipação de calor: equilibre a velocidade do ventilador e o ruído para garantir controle de temperatura a longo prazo.
Qualidade da soldagem: Evite mau contato causado por solda falsa e solda fria.
Tendências da indústria
Miniaturização e alta densidade de potência: como a fonte de alimentação SFX, adapta-se a hosts pequenos.
Controle digital: Use um processador de sinal digital (DSP) para obter uma regulação inteligente de tensão.
Design totalmente modular: os usuários podem personalizar os cabos para reduzir a desordem no chassi.
Por meio do processo acima, as fontes de alimentação de mesa devem passar por rigoroso controle de processo e testes, do design ao produto final, para garantir sua confiabilidade, eficiência e segurança. Marcas diferentes podem diferir em materiais (como capacitores totalmente japoneses), grau de automação (como linhas de produção SMT totalmente robóticas) e padrões de teste.